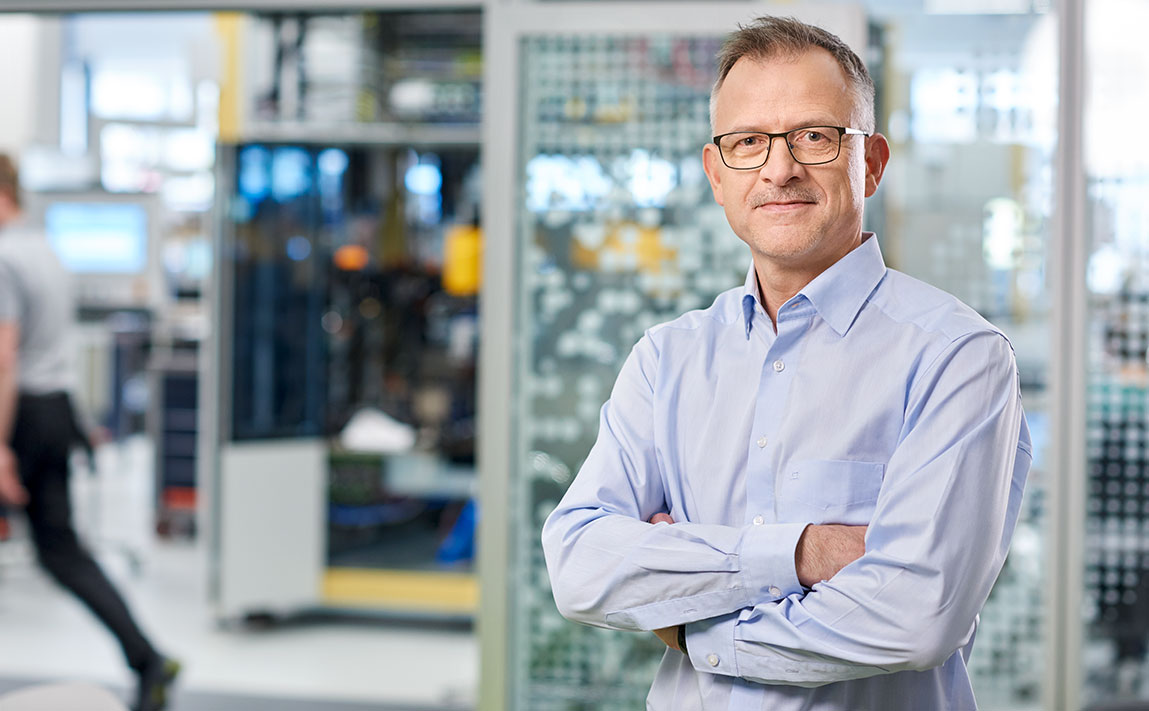
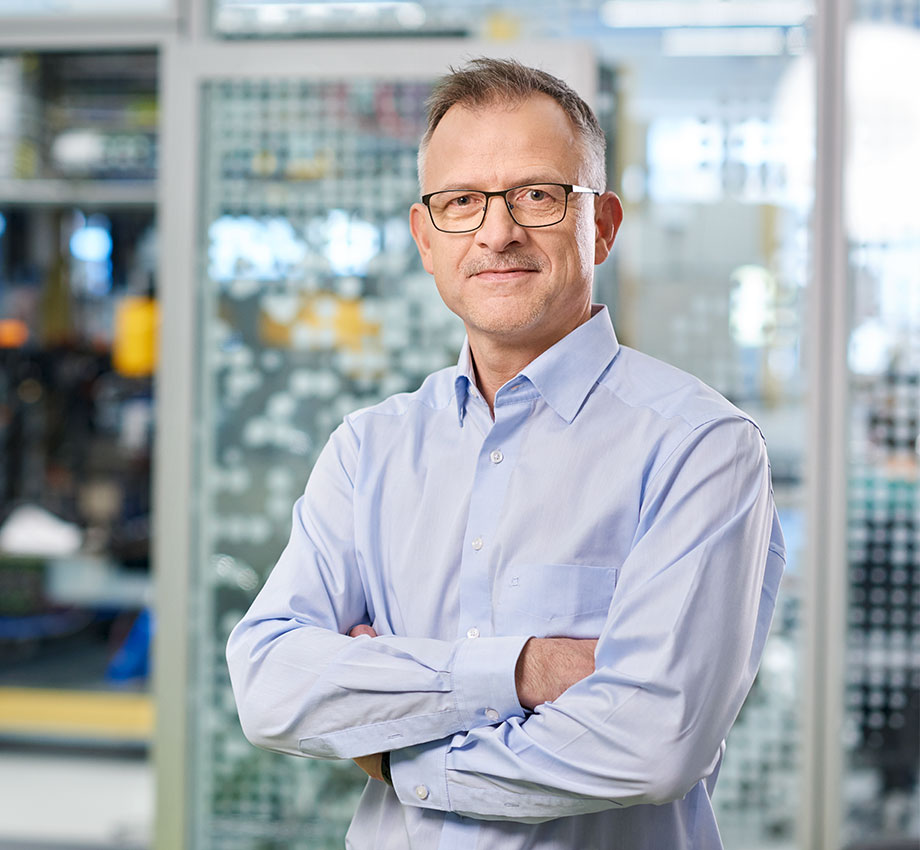
Gerhard Axmann is a qualified mechanical engineer who has worked for the company since 1989. Since 2004, he has worked in central purchasing in the division of Corporate Supplier Development Quality, where he has been responsible for the development of suppliers of turned, milled, and extruded parts.
Responsibility in the Supply Chain
Sustainable from the Start: Putting Suppliers to the Test
Gerhard Axmann Supplier Developer
Scroll DownResponsibility begins here, in our company. But is this also where it ends? For Schaeffler, the answer is a clear no. The company is taking action to ensure social and ecological standards are upheld at its more than 34,000 suppliers worldwide. For Gerhard Axmann, this is a full-time job. He takes a close look at new suppliers, sometimes making unexpected discoveries.
Taking a Closer Look
Our network spans the globe: 34,000 suppliers from around 80 countries provide Schaeffler with the products, processes, and services that the company needs to produce its products. Gerhard Axmann gets involved when new suppliers are to be added to this network. At the age of 56, he knows that Schaeffler depends on good cooperation with its suppliers to be successful. With many of them, the company has maintained multiyear partnerships. Doing this successfully depends decisively on making the right first choice. “Since we are suppliers ourselves, we know that it is not always easy to meet customers’ demands,” Axmann explains. “We must nevertheless be strict with our own suppliers, too, because we have demanding standards and norms when it comes to meeting obligations for sustainability. This requires a good mix of monitoring and trust toward our suppliers.”
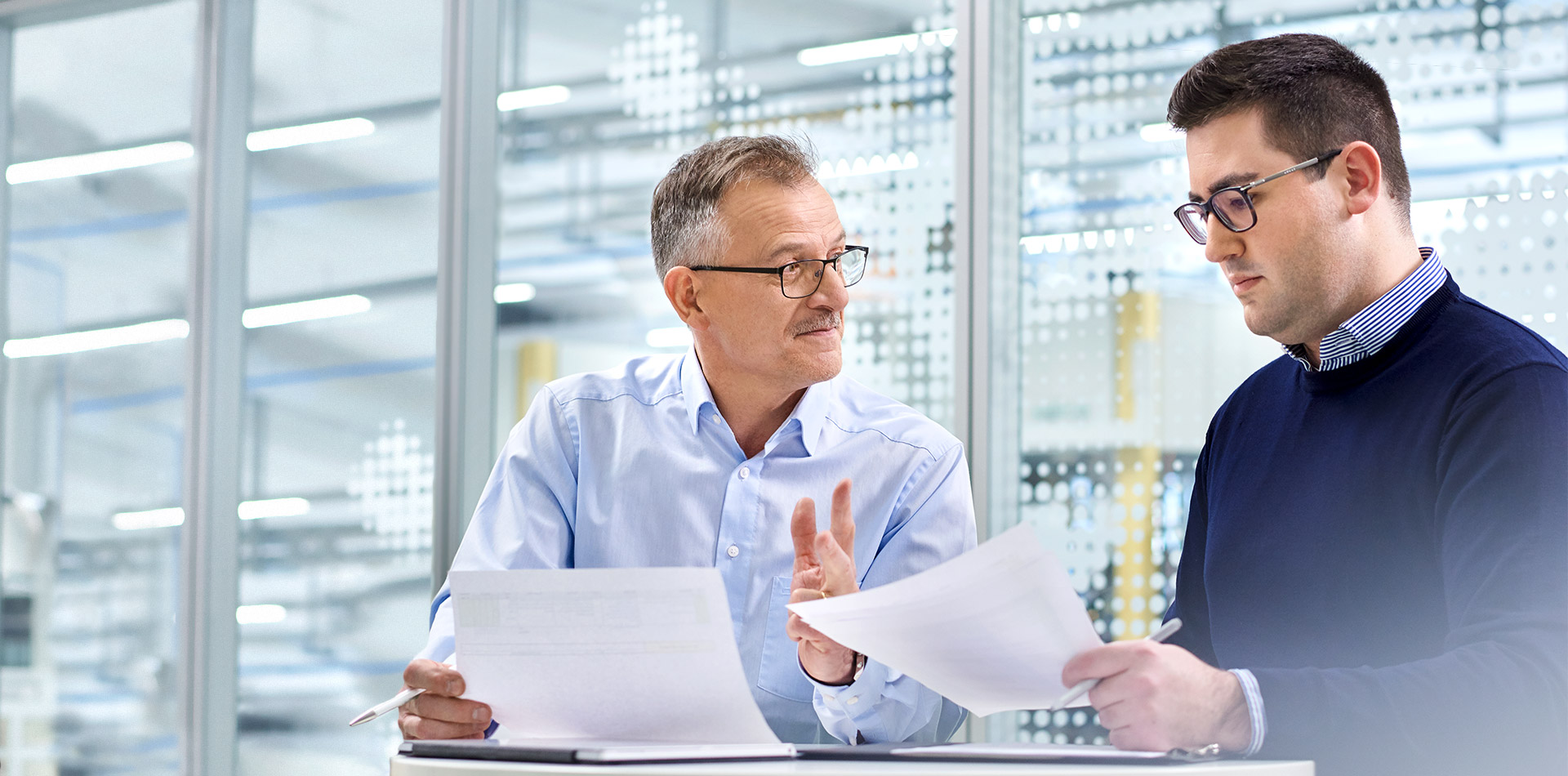
In addition to requirements for the quality of products, processes, and services, or for project management for a potential business partner, the selection of new suppliers must also consider aspects of sustainability. Does the supplier observe the environmental and social standards that Schaeffler has specified in its Supplier Code of Conduct? Does the supplier work with data and information carefully? Axmann and his colleagues find answers to these questions in a multistep selection process that includes an on-site assessment of suppliers in what are called initial assessments (formerly potential analyses).
Following a supply request – from a Schaeffler site, for example – the application process begins. Potential suppliers are accepted into the selection process only after they have sent or approved requested certificates as well as various contractual documents to our quality and environmental management systems and thus signaled their interest in working together. The application then leads to the initiation of an on-site assessment, which is where Gerhard Axmann takes over. For the engineer, this means packing his bags. He travels around 100 to 120 days a year. In order to thoroughly inspect new business partners, he visits the production sites directly. Things don’t always turn out as planned. “Unfortunately, especially earlier, we sometimes also experienced dangerous and almost bizarre things,” he recalls. “In the production site of a supplier of forged components, we once witnessed how little consideration was being given to occupational safety. The employees were wearing sandals, used no ear protection, and transported the glowing pieces of steel from one forming press to another without any kind of protective measures. We had arrived only for an initial discussion, which we then immediately ended.”
Gerhard Axmann travels around 100 to 120 days a year. In order to thoroughly inspect new business partners, he visits the production sites directly.
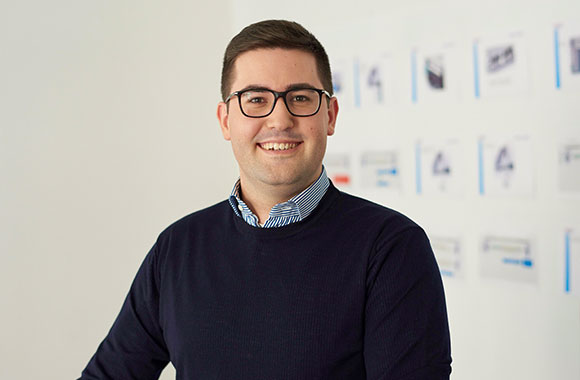
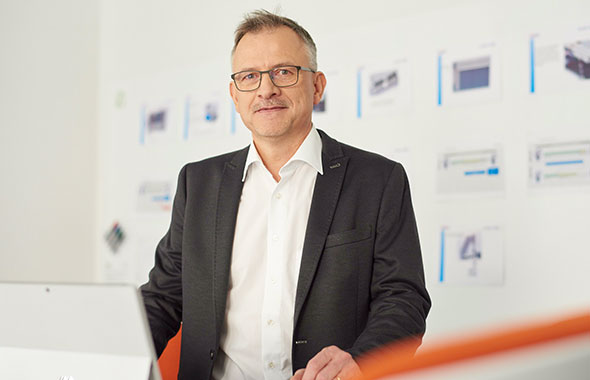
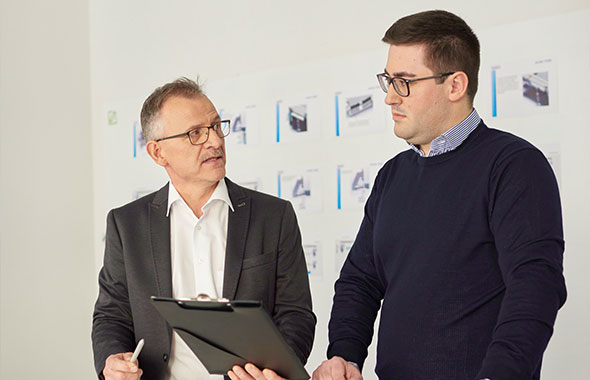
Today, Axmann and his colleagues increasingly often make use of the records of such initial discussions. If a business area needs a new supplier, a purchaser or a supplier developer is sent to carry out a first, structured quick assessment, or pre-assessment. This allows them to get an overview of the supplier. And it saves a lot of time, since a comprehensive assessment, the initial assessment, takes at least two days. In the process, Axmann goes through an extensive questionnaire, examines processes and documentation, and visits the entire production site. “We have eyes and ears everywhere,” he says with a grin. “And we don’t limit our discussions to our main point of contact but also speak with employees from the various areas of expertise. This allows us to find out how the company really works.” In the evaluation that follows, Axmann gives a score of one to ten for each topic area that was assessed. A ten means that the supplier can completely meet requirements. If this is not the case in one area, a plan of action is subsequently prepared and then worked through.
Transparency
The supplier is thus given the opportunity to improve. For strike-out questions, a score of less than ten points means the preliminary end of the selection process. In other words, the process is placed “on hold” until the open issues have been remedied by immediate action. These include the question of whether the supplier can guarantee that water, air, and soil will not be polluted or negatively impacted by its business activities.
Observing social and ecological criteria all along the value chain is an important part of corporate responsibility for Schaeffler. These aspects are therefore specified in the company’s guiding principles and its Supplier Code of Conduct. Companies that sign the Code commit to respecting human rights, treating the environment responsibly, and making efforts to support the safety and health of their workers.
“For us, responsibility doesn’t stop at the factory gates.”
Gerhard Axmann
On the one hand, sustainable supply management means recognizing risks in business relationships early on. And on the other hand, it is also a response to growing expectations from outside the company – national governments are making increasingly strong demands of companies to take responsibility for what happens outside their own plants. We have thus been providing reports for years in accordance with requirements about conflict minerals, enabling our customers to fulfill the legal requirements they face. As part of their own sustainability programs, Schaeffler’s customers also increasingly require proof of how their precursor products were made.
In order to make supplier evaluations more comparable to each other and achieve more transparency in the supply chain, Schaeffler works together with other companies in our industry, for example, with members of the working group “Sustainability in the supply chain” of the German Association of the Automotive Industry. In this working group, sustainability experts from producers and suppliers develop standardized, industry-specific sustainability questionnaires for on-site assessments, among other things.
Gerhard Axmann sees many advantages to this cooperation: “We all face similar challenges in selecting suppliers. This is why it is important that we address structural problems together and learn from each other.” This might not only make his work easier but also create better conditions for the people and the environment in production countries.
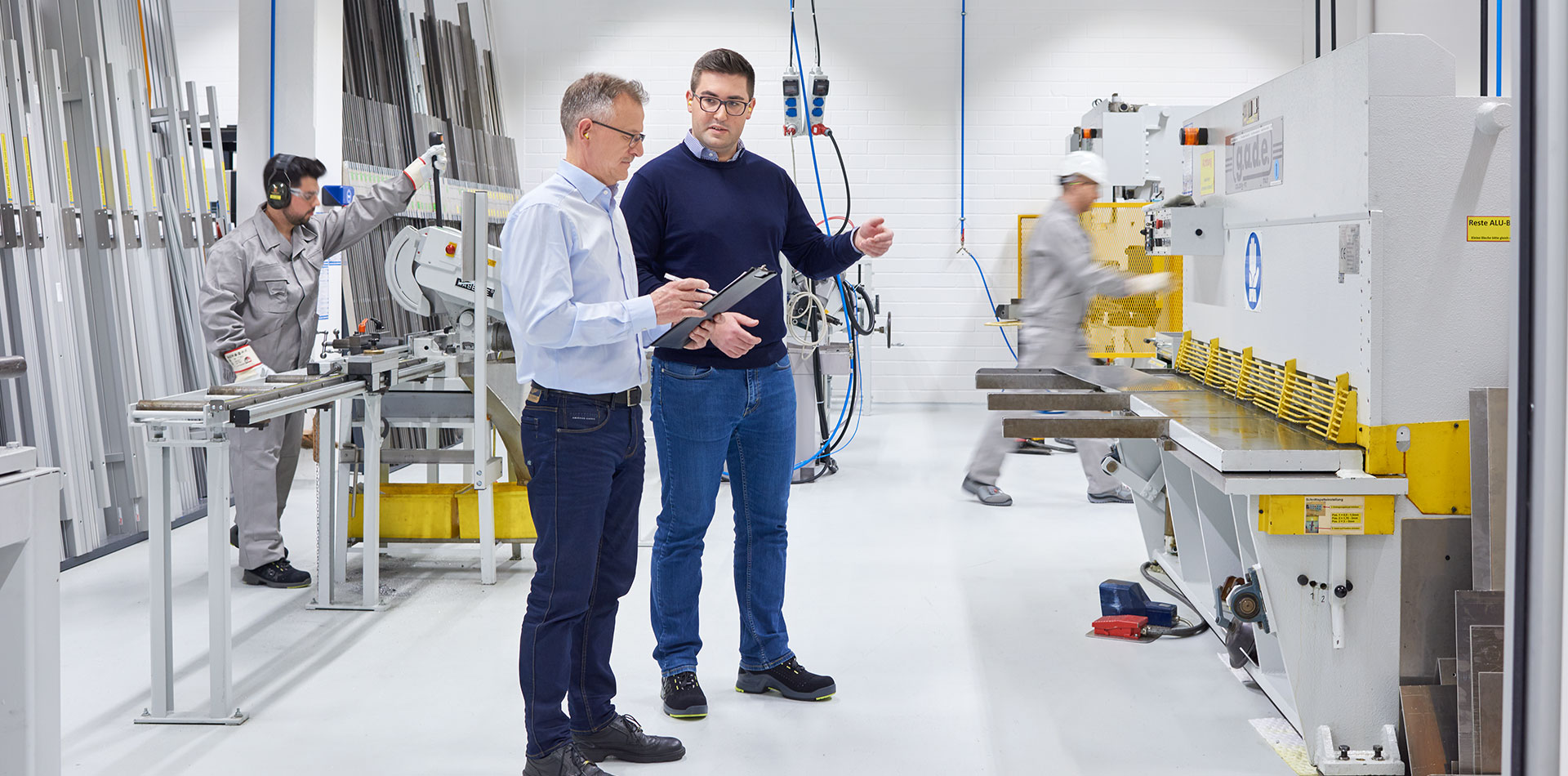