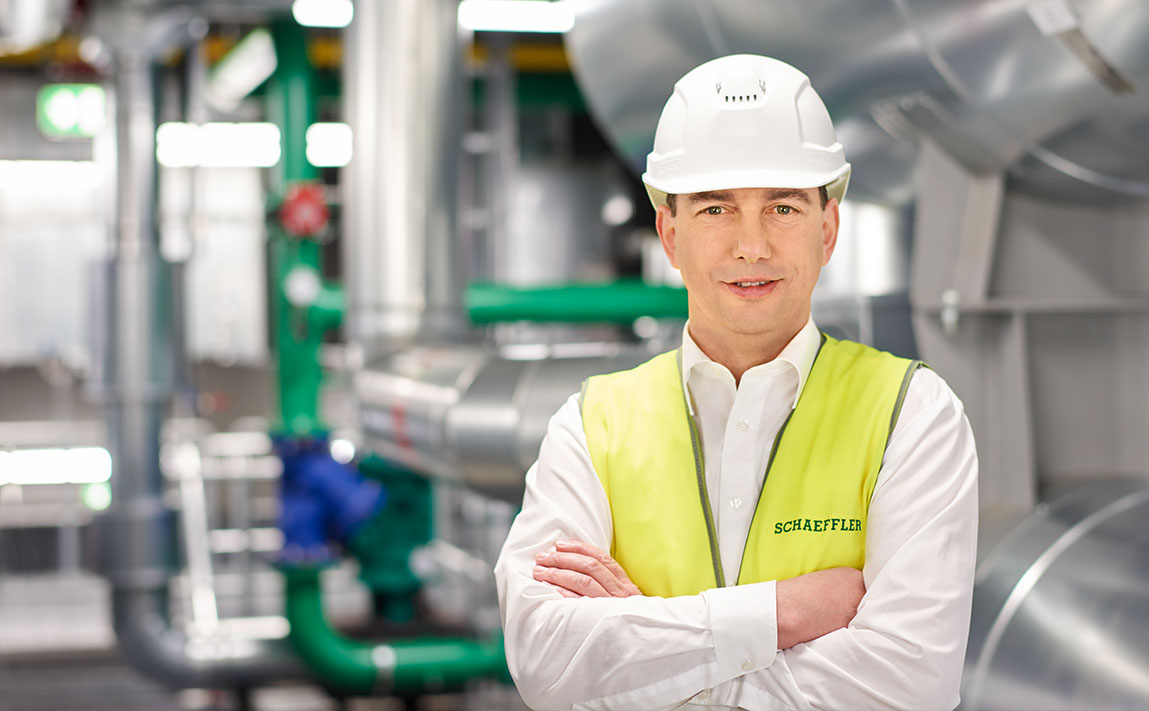
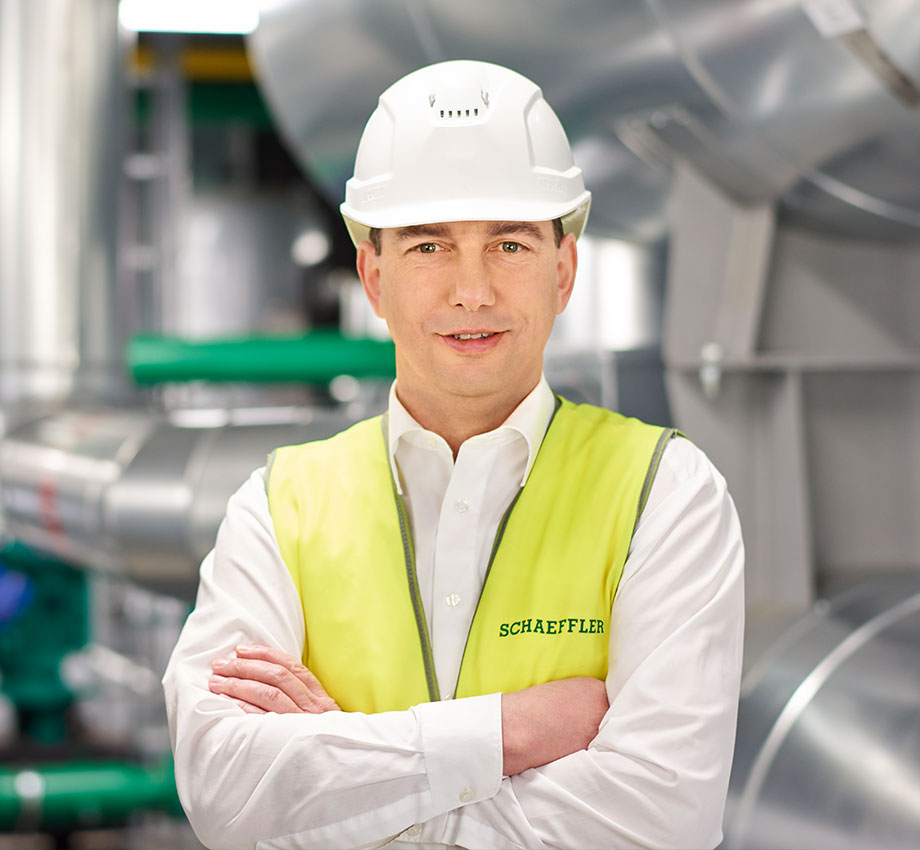
Matthias Behr studied heating, ventilation, and climate engineering in Regenstauf. He has worked at Schaeffler since 2000, and since 2013, he has been Head of Supply Engineering (Building & Processes) in Corporate Construction, Energy Management & Maintenance in Herzogenaurach.
Commitment to Climate Protection
Multitalented for More Energy Efficiency
Matthias Behr Head of Supply Engineering
Scroll DownOur aspiration aims high: Schaeffler intends to continuously improve its own energy efficiency. This is a goal Matthias Behr is working toward. The engineer and his team have built a total of four cogeneration plants over the past two years at the production sites of Herzogenaurach and Homburg. The power plants are not only capable of producing electricity and heat but are also used for cooling. They are thus one of the most efficient ways of supplying Schaeffler sites with energy.
Triple Benefit
“Cogeneration units are truly multitalented,” says Matthias Behr. For the last four years, Behr, an engineer, has worked at Schaeffler as Head of Supply Engineering (Building & Processes). In this role, he has spent the last two years directing the construction of four cogeneration units (also called combined heat and power units, or CHP) in Herzogenaurach and Homburg. “What’s innovative about our CHPs is that we don’t just use them to generate electricity and heat but also cold water that we use to cool our buildings and production facilities,” he explains with excitement. This triple benefit is made possible thanks to the principle of cogeneration, which links the production of power, heat, and cooling. In the process, the heat generated in a CHP is used, among other things, to operate what are called absorption chillers. These are used in turn to cool office and production buildings at the three production sites. “In this way, we were able to increase the security of our energy supply and also replace some of the existing cooling units that used much more energy,” Behr happily reports. “That makes complete sense not only in terms of efficiency but also for business.”
“Cogeneration units are truly multitalented.”
Matthias Behr
The CHPs were put into service in Herzogenaurach and Homburg at the end of 2016. It was in Herzogenaurach that Matthias Behr and his team conducted the first studies in 2014 to determine the feasibility and profitability of on-site CHPs. “The positive results of our studies convinced everyone. Between 2016 and 2017, we then installed two units on-site.”
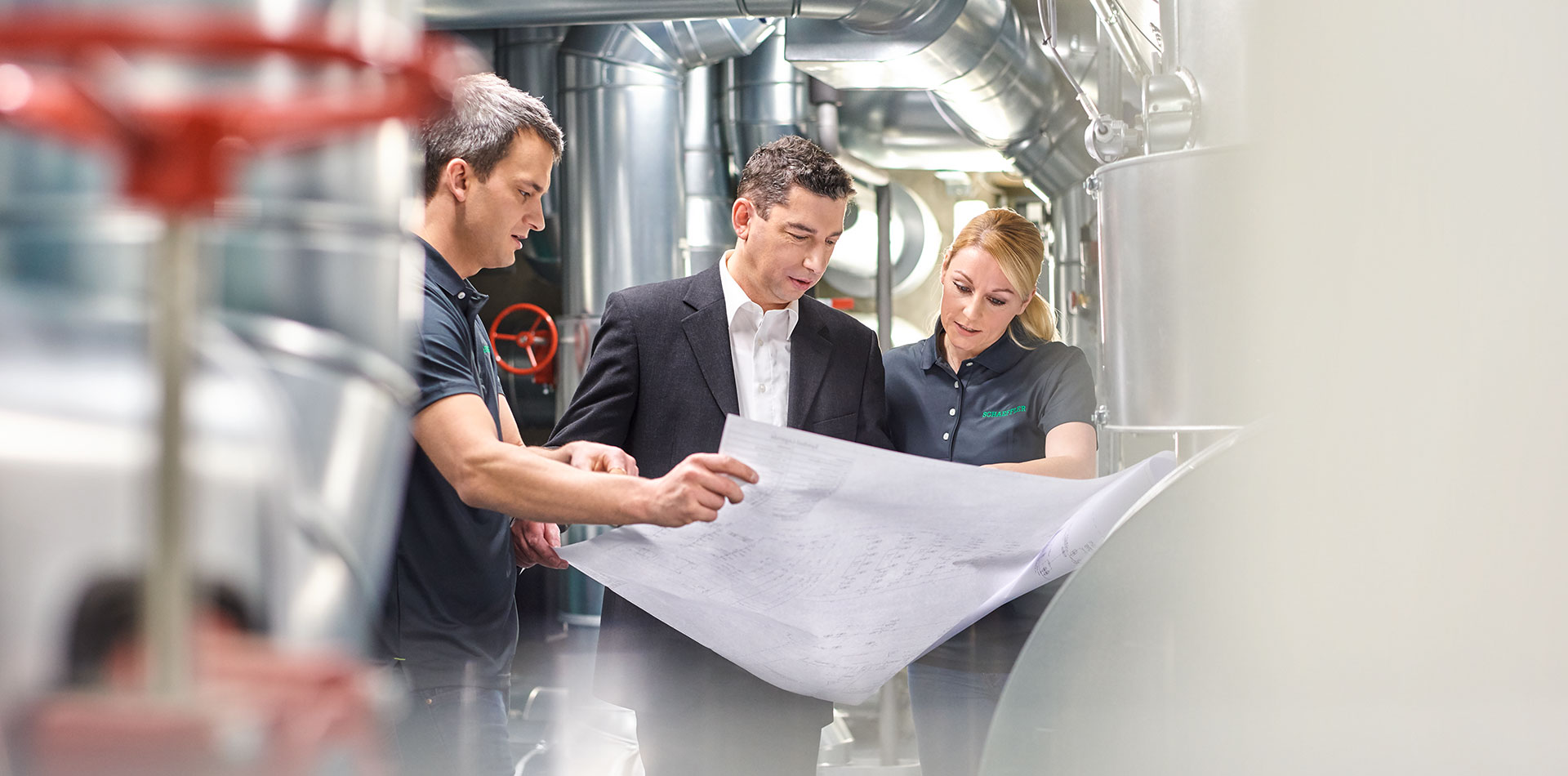
Matthias Behr has spent the last two years directing the construction of four cogeneration units (CHP) in Herzogenaurach and Homburg.
Pretty fast – especially if you consider that no less than 8,300 meters of heat pipes and 5,600 meters of cold-water pipes for cooling had to be installed, and that the buildings being connected to the system had to be transitioned from steam supply to hot water supply. In order to supply the buildings in Herzogenaurach, these pipes carry as much as 155,000 liters of water an hour in the heating system and 459,000 liters of water an hour for cooling operations. That is approximately as much as 333 50-meter swimming pools.
Another reason the construction was challenging for Matthias Behr was the need to ensure that all connected production systems would be provided with energy. An outage in the energy supply would have resulted in a production stop that would have then been very costly. “But the team was fantastic in how they planned and worked,” he says. “Everything worked out seamlessly.”
Climate Goal
The new units are impressive even from the outside: a bright building with ten futuristic-looking reservoirs on one side. Inside, the buildings house state-of-the-art technology. “Thanks to their use for cooling, the units achieve an efficiency rate of more than 87%,” Matthias Behr reports. This high degree of efficiency confirms that the technology operates extremely efficiently in comparison to the conventional forms of generating power.
This kind of modern and efficient energy supply is an important building block in Schaeffler’s climate strategy. It’s obvious that large production sites use a lot of energy – which is why Schaeffler believes it has the responsibility as a global manufacturing company to find solutions for dealing with climate change. Yet the operation of cogeneration units is just one of many steps that Schaeffler is taking to reach the climate goal it has set for itself. By 2025, it intends to reduce its emissions by a total of 360,000 t of CO2 in comparison to the base year of 2015. Other measures also contribute to reaching this goal – for example, the introduction of comprehensive energy management or the networking of machines by means of Industry 4.0 technology so that they work even more efficiently.
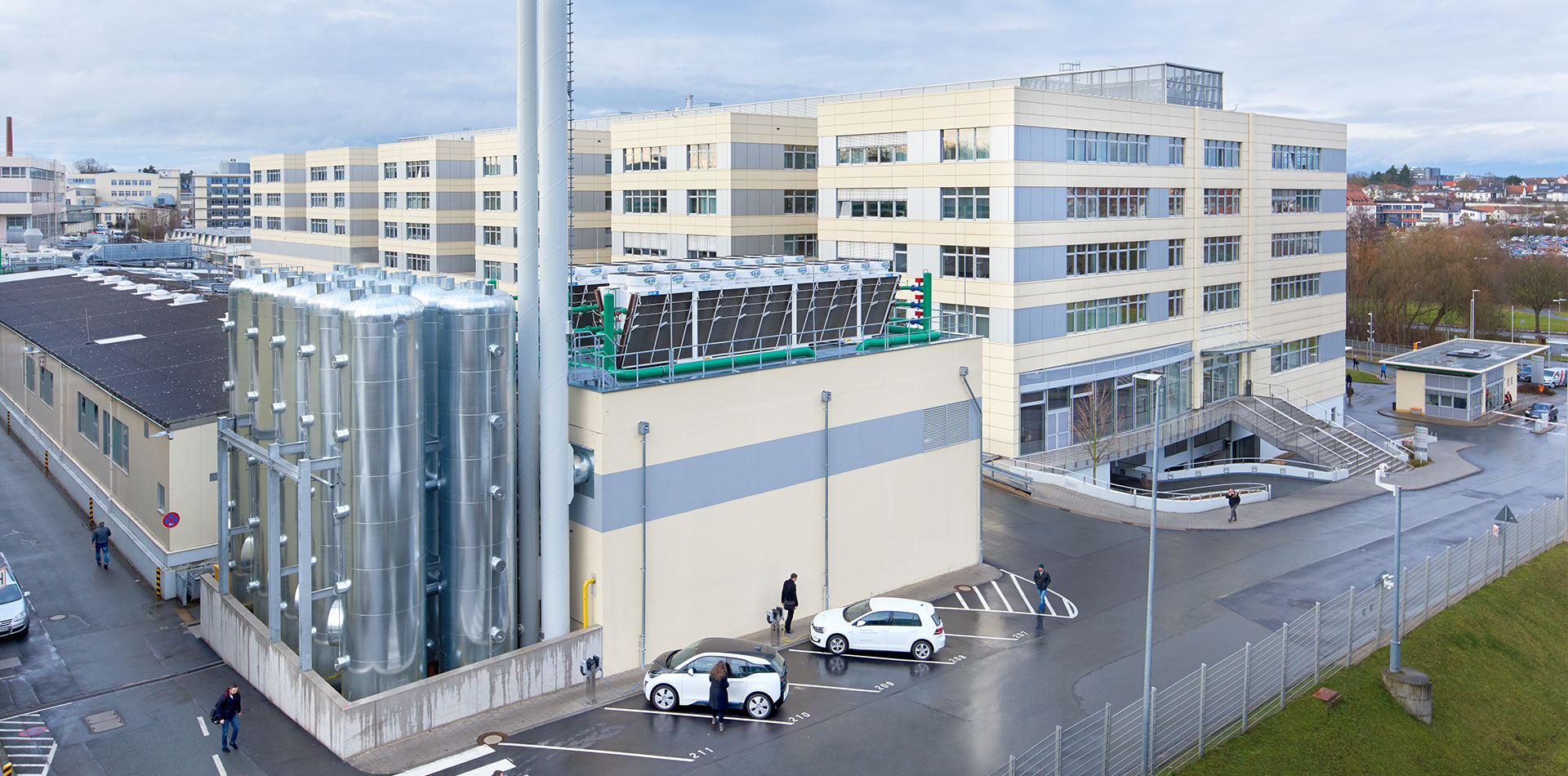
Outside the CHP in Herzogenaurach, charging stations can provide electric vehicles with green energy from municipal sources.
Matthias Behr knows, “We are also engaged with other energy generation technologies and carefully assess which technologies make sense for which production sites. For example, it’s easy for me to imagine that we will more heavily employ renewable energy in the future – perhaps the same kind of pholtovoltaic systems you find on the roofs of private houses. This technology offers a lot of potential.”