Out of the crisis: Stronger together
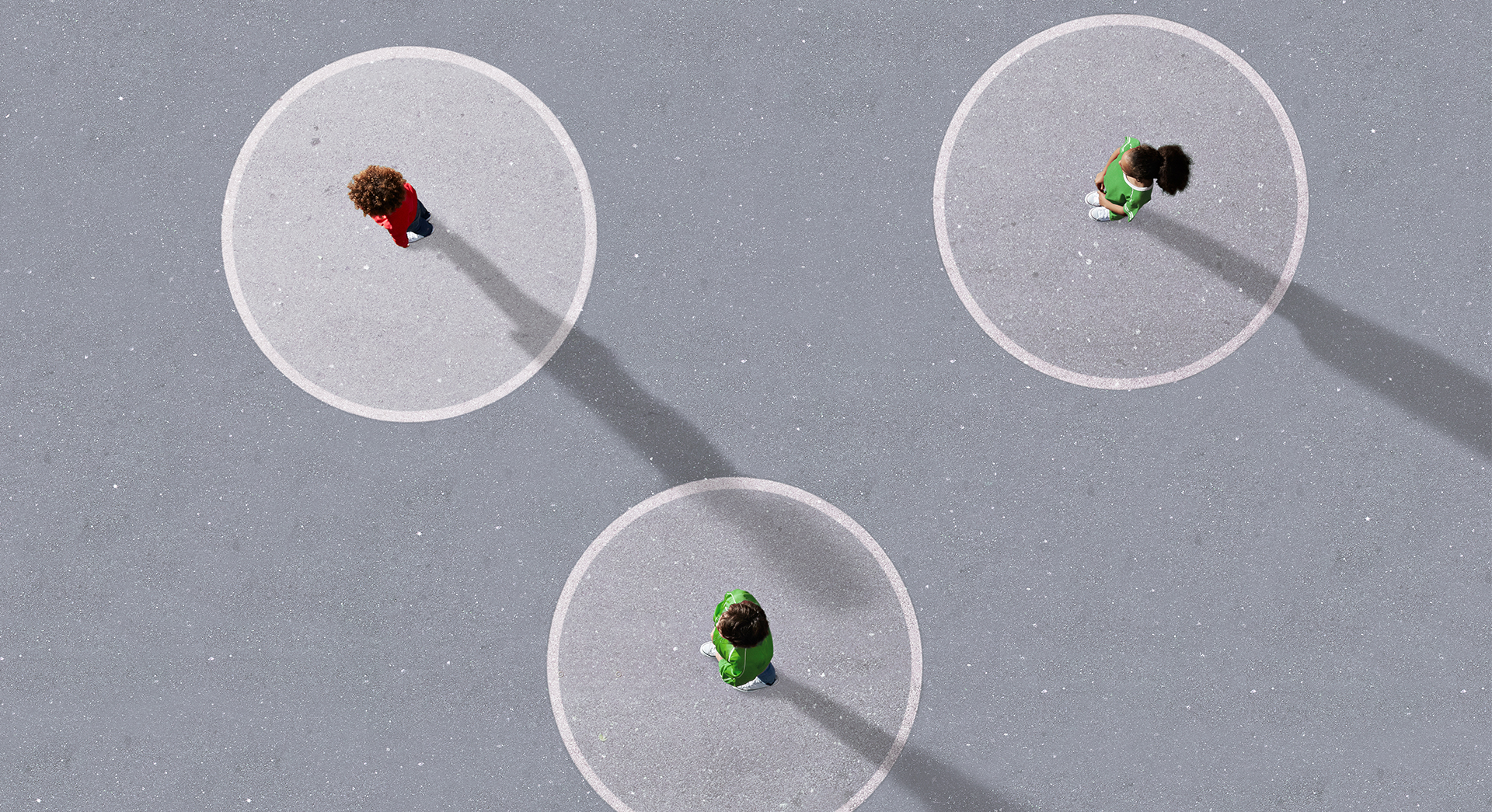
Schaeffler assumes social responsibility and does its part to mitigate the coronavirus pandemic, thus protecting employees, maintaining business operations, and minimizing social consequences. Collaborative partnerships with suppliers and customers as well as digital tools for supply chain management have helped Schaeffler avoiding supply shortages.
Managing the crisis
The coronavirus pandemic is pushing people and companies to their limits, calling for pragmatic solutions and collaboration. Schaeffler plays an active role in mitigating the crisis. All locations have consistently introduced measures to reduce the risk of infection. In addition to distancing and hygiene rules, these measures also include redesigning workstations and enabling employees to work from home.
At Schaeffler, well-functioning crisis management is primarily the result of early collaboration across divisions and between central, regional, and local units and functions. Business processes were adapted without the weight of bureaucracy and, in some cases, within a very short period of time. For example, Schaeffler has been producing its own face masks for its employees at its plant in Taicang, China, since spring 2020, for which a fully automated production line was planned and implemented in just five weeks. 3D printing capacities at the company’s locations in Mexico, Germany, and Turkey are also used to produce face shields.
More information on crisis managementface masks are produced every day at Schaeffler
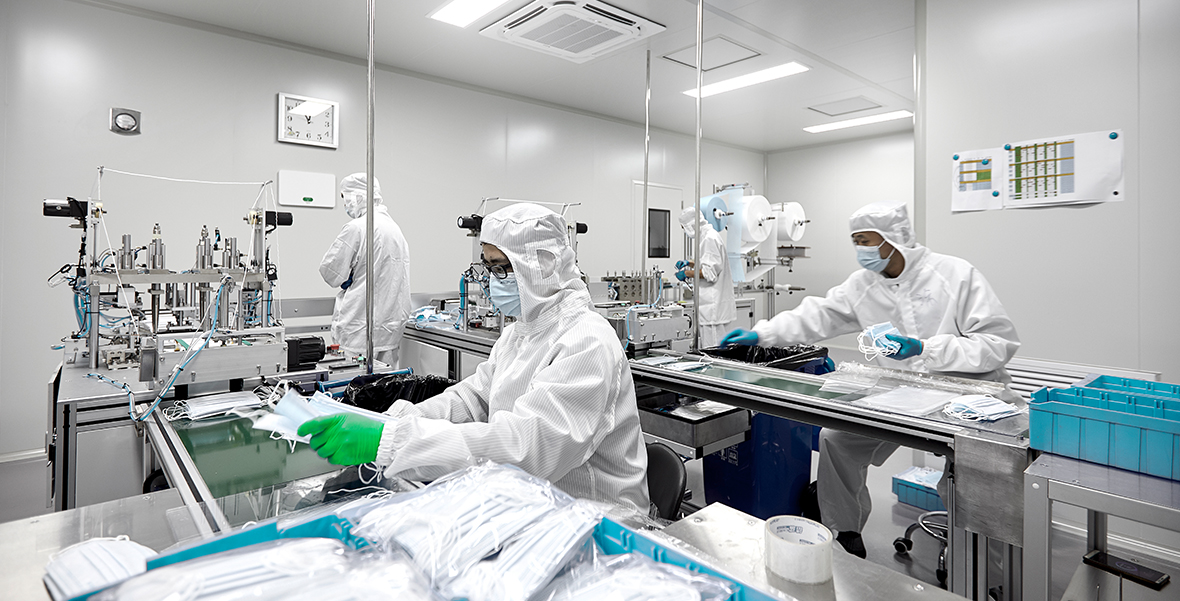
Schaeffler has been producing its own masks in Taicang, China, since spring 2020.
Securing the supply chain
Thanks to its diversified, global production network, Schaeffler can compensate for local shortages by means of redistribution, a benefit that can provide stability during the coronavirus pandemic and other crisis situations. Since Schaeffler needs to be able to analyze its supply chains in real time, so that it can anticipate potential shortages and respond promptly with mitigation measures, the company introduced the Risk Tower, a tool that helps to digitally secure supply chains. All relevant information converges at virtual supply chain control centers and activates an alarm any time a potential shortage is identified. However, digital analysis cannot replace personal exchange. Close coordination with its suppliers and contacts – e.g. in the form of regular supplier conferences that are now held digitally – also helped Schaeffler to avoid supply shortages.
More information on supplier managementdelivery thanks to secured supply chains
Mitigating social consequences
The coronavirus pandemic has put health and social systems around the world to the test, to its limits, particularly in emerging and third-world countries. For example, rural communities in India have only limited access to timely health care. In order to improve the situation for the disadvantaged communities in Vadodara and Pune, Schaeffler India has launched the Mobi-Health initiative through its CSR program HOPE. Mobile health units play an important role in ensuring the provision of free, basic medical care for those in need in more than 80 villages.
More information on corporate citizenshiphave been donated to organizations and social institutions to mitigate the consequences of the coronavirus pandemic.
Together for more climate action
Effective climate protection requires a high degree of agility and adaptability. As one of the world’s leading automotive and industrial suppliers, Schaeffler develops solutions and components for ...
Navigating the digital future together
For Schaeffler, the digital transformation is an engine for new processes, innovations, and business models. Sustainable product solutions are at the heart of the transformation – which involves ...