Green Products
- Sustainability aspects are considered during the product development phase
- The company is working with partners to develop a hydrogen fuel cell
Part of NFBThe Schaeffler Group defines Green Products as those products whose production, transport, use, and disposal are responsible for less CO2e emissions than those of their substitutes. CO2e reduction is integrated into the product development process, which includes product design and material selection. The entire life cycle takes center stage, from the extraction of raw materials and production to product use and potential circular economy concepts at the end of the service life.Part of NFB Ende
Product carbon footprint (PCF)
Part of NFBThe Schaeffler Group conducts life cycle assessments (LCA) to measure the environmental impact of its products throughout their entire life cycle. Based on the ISO 14040 and ISO 14044 standards, internal guidelines were developed to regulate LCA administration, processing, reporting, and more for the entire life cycle. These methods were certified by TÜV Rheinland. The LCAs serve as a key tool for documenting the sustainability performance of products and processes, with a particular focus on the product carbon footprint (PCF). LCAs also enable analysis of the supply chain and production and identify suitable reduction measures. When conducting LCAs, the Schaeffler Group usually uses the system limited to the cradle-to-gate approach (primarily material and production). In special cases, aspects of the cradle-to-grave (plus use phase) and cradle-to-cradle (plus circular economy) approaches are also taken into account.
In parallel to this certified method, the Schaeffler Group has also been using additional tools to calculate the carbon footprint throughout the development process since 2022. A tool already used for cost-value analysis is currently being expanded to include a calculating metric for the carbon footprint and combined with corresponding databases, which makes it possible to efficiently prepare calculations for a whole host of products and integrate them into the product development process early on. The central database contains suppliers’ emission factors, including the data of steel suppliers, with additional emission factors, suppliers, and material groups to be added over time. Training courses on the topic of “Design for Environment” are also being developed to acquaint employees with the opportunities provided by sustainable product development in particular.
The PCF comes into play during the design phase of product development. Take for instance innovative roller bearings. At present, each PCF is determined individually using LCA software, but there will be an automated calculation option available in the product configurator for roller bearings (Medias-®) as of 2023.Part of NFB Ende
Automotive Technologies
Part of NFBThe Automotive Technologies division partners with the global automotive industry for passenger cars and commercial vehicles in developing and manufacturing components and systems for all-electric and hybrid powertrains, the fuel cell powertrain, as well as for internal combustion engines and chassis systems. The division also offers a wide range of rolling bearings that is largely powertrain-agnostic. The Automotive Technologies division manages its business based on the four Business Divisions (BDs) E-Mobility, Engine & Transmission Systems, Bearings, and Chassis Systems which in turn comprise several business units.
Automotive Technologies division
In the Engine and Transmission Systems business division, additional synergies are being developed for the powertrains of internal combustion engines. The new Bearings business division bundles the extensive application and product portfolio of roller bearings in order to take advantage of synergies in a highly competitive environment, promote innovations, and generate growth in new markets. A new division structure should also continuously promote expansion of the E-Mobility and Chassis Systems business divisions. Reorganizing business divisions and overhauling the product portfolio of the Automotive Technologies division is part of the divisional subprogram of the Roadmap 2025.Part of NFB Ende
E-Mobility
Part of NFBThe Schaeffler Group is developing a variety of components and system solutions for electric mobility, with a portfolio that ranges from powertrains for hybrid and all-electric mobility to fuel cells.
The company’s most sophisticated drive system to date for all-electric vehicles is the new 4-in-1 electric axle, which integrates the electric engine, power electronics, transmission, and thermal management into the axle drive. The 4-in-1 electric axle not only boasts a compact design, but also improves the interplay between the subsystems. Efficiency up to 96% is possible in an optimally designed system, with each additional percentage point increasing the range.
Especially thermal management has a significant impact on vehicle efficiency and comfort. The Schaeffler Group combines the thermal system with the drive components of a traditional electric axle, which are usually viewed as two separate entities, creating a highly integrated, compact overall system that requires much less space than non-integrated solutions. Because unnecessary tubes and cables can be eliminated, less energy is lost in the form of heat. Intelligent control of thermal management also ensures that excess heat is efficiently diverted from power electronics and the electric engine and can be used in the vehicle interior.
The Schaeffler Group has further improved efficiency with a new heat pump that works with the natural gas carbon dioxide, which has a much lower environmental impact than conventional coolants. Carbon dioxide also boasts physical properties that make vehicle heating more efficient.Part of NFB Ende
Examples of electric mobility products
With its expertise and product portfolio in the electric mobility sector, the Schaeffler Group is doing its part to decarbonize commercial vehicles. The new range of water-cooled 800-volt motors available in 2023 is not only scalable and efficient, but also exceptionally robust.
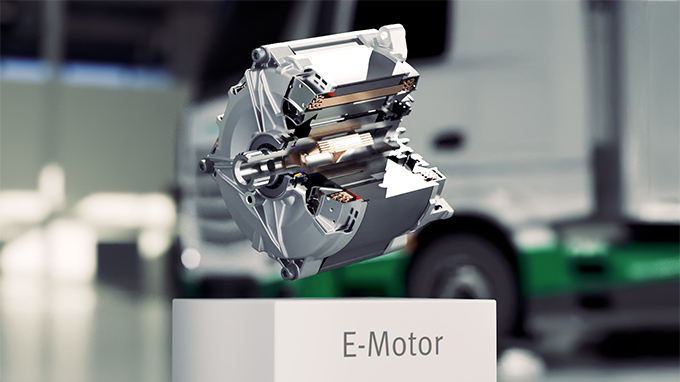
Engine and Transmission Systems
Part of NFBNew cars with internal combustion engines will continue to be produced in the coming years. The Schaeffler Group’s goal is to make this drive as efficient and resource-friendly as possible, offering solutions for consumption-optimized internal combustion engines. The Schaeffler Group uses an extensive modular kit of technologies and products that, depending on requirements, can be mixed and matched to maximize efficiency. For example, the Schaeffler Group uses the combination of electric cam phasers and the newly developed eRocker System for highly variable valve control. In full hybrid applications, this variability delivers high efficiency in the interaction between engine and innovative transmission, enabling a reduction in CO2 of around 10% – while maintaining the same engine power and lower exhaust emissions. The Schaeffler Group’s innovative vibration damping solutions ensure this potential can be exploited throughout all applications.Part of NFB Ende
Bearings
Part of NFBBearings play a key role in the safety and efficiency of future vehicles and offer enormous savings potential especially for commercial vehicles – whether electric or gas-powered. That is why the Schaeffler Group is developing special bearing solutions for an efficient powertrain that reduces wear on light commercial vehicles and even more so on heavy commercial vehicles and thus decreases resource consumption and CO2 emissions. Particularly for commercial vehicles, the Schaeffler Group has developed a wheel bearing unit that further reduces friction loss. For a 13-ton rear axle, for example, the unit reduces friction by 56% and loss by up to 600 W. For a commercial vehicle with an electric range of 500 km, that results in energy savings of up to 11 kWh for each charge, meaning a battery of the same size would enable a longer range. Alternatively, the same range can be achieved with less resources and at a lower cost.
Another bearing innovation of the Schaeffler Group is the high-performance ball bearing with integrated centrifugal disc. The special feature of this bearing, which is unique in the world, is that the rubber seals which are normally firmly fixed to the outside of sealed bearings are replaced by a specially developed centrifugal disc in the inner ring.
Much like a sealed bearing, the centrifugal disc keeps contaminants out. But because the disc rotates freely, the bearing generates about 80% less friction than with conventional seals, resulting in a CO2 reduction of up to 0.3 g per kilometer per vehicle. Reducing losses by up to 30 W per bearing can also improve the range of electric vehicles by up to 1%. The centrifugal disc bearing also lasts considerably longer. Compared to an open bearing, the service life can increase by a factor of up to ten, whereas the unit lasts twice as long as conventional sealed ball bearings. As a result, both the bearings and the transmission can be smaller in the future, thereby conserving material and weight.Part of NFB Ende
Examples of bearing products
To make product and passenger transportation more effective and sustainable, the Schaeffler Group offers special bearing solutions for an efficient powertrain that reduces wear on light commercial vehicles and even more so on heavy commercial vehicles and thus decreases resource consumption and CO2 emissions.
Chassis systems
Part of NFBThe Schaeffler Group is helping to transform mobility, including for new chassis applications that, for example, enable highly automated driving. Take for instance the steer-by-wire technology, a type of steering that eliminates the rigid connection between steering wheel and steering gear, opening up new design opportunities for vehicle interiors. The system also increases driving safety and comfort. And because steer-by-wire systems no longer have a mechanical connection between the steering wheel and steering gear, the steering wheel can be replaced with a joystick, for example, allowing people with physical disabilities to maintain their mobility. Thanks to the interplay between the brakes, environment recognition, and the steering system, the steer-by-wire systems of future vehicle generations will also increase safety.
In recent years, the Schaeffler Group has developed extensive expertise in chassis systems. The Chassis business division views itself as a link between chassis systems for large-series automotive production and new forms of mobility, as revealed, for example, by the first series rollouts of the mechatronic intelligent rear wheel steering (iRWS) and the development of a hand wheel actuator (HWA) with force feedback module.Part of NFB Ende
Automotive Aftermarket
Part of NFBThe Automotive Aftermarket division is responsible for the Schaeffler Group’s worldwide spare parts business for passenger cars and commercial vehicles and supplies innovative repair solutions in original-equipment quality. The company is thus helping to increase the service life of vehicles. Demand in the spare parts business is primarily influenced by three factors: the rising number of cars around the world, the increasing average age of vehicles, and growing vehicle complexity. These factors boost the demand for repair, which requires increasingly advanced repair solutions and services for workshops.
The portfolio offers an extensive selection of repair solutions and individual components for all vehicle classes, with a focus on expanding the range for full hybrids and plug-in hybrids. For many hybrids, the spare parts program encompasses a comprehensive portfolio of individual components and complete KITs for all key engine systems.1) For hybrid vehicles, the division covers more than 85% of chassis and engine components.
E-Mobility solutions are introduced in the aftermarket in close collaboration with the Automotive Technologies division. Trends such as electric and increasingly automated transmissions, autonomous driving, and the circular economy have a foreseeable influence on how vehicles will be used and serviced in the future.
Thanks to the Schaeffler E-Axle RepSystem – G, workshops can properly repair new electric aggregates for the first time, rather than replacing them entirely, which can be expensive. The cost of repairing a transmission is only about 20% of that of a complete replacement.Part of NFB Ende
Industrial
Part of NFBThe Industrial division develops and manufactures precision components, both rotary and linear bearing solutions, drive technology components and systems, as well as service solutions such as sensor-based condition monitoring systems for a large number of industrial applications.
Through the divisional subprogram of the Roadmap 2025, the Industrial division is focusing on growth and expansion of the core business, the scaling of the service business, and development of new business fields in growing markets, with global production and overhead structures as well as sales and delivery processes overhauled in the process.
The product portfolio is divided into eight sector clusters: wind, aerospace, rail, off-road, two-wheelers, raw materials, power transmission, and industrial automation. Products are sold directly to end customers or through machine and plant manufacturers, trade partners, or service providers. The sector clusters are in turn divided into four market clusters: renewables, transportation and mobility, machinery and materials, and industrial automation.
Customer and product portfolio in the Industrial division
In terms of bearing solutions, the product portfolio for the core business primarily contains rolling and plain bearings, and linear guidance systems. This portfolio covers a wide spectrum, from high-speed, high-precision bearings with a diameter of 4 mm to larger bearings with a diameter of 4,200 mm. Bearings are used in all sectors, while linear guidance systems are primarily used in machine tools in the industrial automation sector cluster. Bearing solutions and linear guidance systems have always formed an essential basis for future growth in the division and are continuously optimized with technical advice and customer-specific products in order to further expand this core business in the individual sector clusters.Part of NFB Ende
Renewables
Part of NFBAs a partner of the energy industry, the Schaeffler Group supplies key components for the expansion of renewable energy production. Efficient bearing solutions boost energy production and the level of efficiency.
The wind industry strives to minimize the cost of generating electricity. The reliability and durability of the bearings play a key role in making energy generation economical. Every bearing failure leads to a loss in energy generation as well as complex repairs and part replacement.
The Schaeffler Group’s large tapered roller bearings have undergone slip-free induction2) hardening for some years now, which significantly improves the carbon footprint, as the bearing rings are always heated locally with renewable energy. Take for instance the tapered roller bearing showcased at the 2022 WindEnergy trade fair. CO2-reduced steel, higher material utilization, and induction hardening can reduce the bearing’s carbon footprint by 70% to 1.5 kg of CO2 per kilogram of bearing.Part of NFB Ende
Transportation & Mobility
The Transportation & Mobility market cluster represents a range of solutions that the Schaeffler Group offers for the aerospace, rail, off-road, and two-wheeler sector clusters. For rail transport, the Schaeffler Group develops and produces new product solutions with optimized functions, high energy efficiency, an extended service life, and longer maintenance intervals.
Designed for an axle weight of up to 25 t, the improved wheelset bearing housing was introduced in 2022 at InnoTrans, the leading trade fair for railway transport. Weight reduction of 14% not only enables heavier payloads but also reduces production-related CO2 emissions.
With development of the TwinTandem, ball bearings generate much less friction, which leads to lower temperatures even at high speeds and thus increases the service life of the greases used and the wheelset bearing as a whole. Comprehensive studies with Schaeffler’s BEARINGX calculation tool reveal a geometry-related reduction in friction of 55% compared with conventional tapered roller wheelset bearings, which lowers CO2 emissions in operation.
The TwinTandem development project is embedded in the “Gearbodies” project supported by the European Commission. In June 2022, the Schaeffler Group and the consortium received the Best Paper Award for the study “Extending the lifetime of journal bearings for high-speed trains” at the World Congress of Railway Research in Birmingham.
Machinery & Materials
Part of NFBIn the Machinery & Materials market cluster, the Schaeffler Group is continuously working to develop solutions for optimizing friction and extending the service life of roller bearings, which also includes the remanufacturing of roller bearings. Due to high capital intensity, optimized machine operation is of the utmost importance particularly for the “raw materials” sector cluster. The Industrial Lifetime Solutions department, whose products and services are also used in other market clusters, specializes in intelligent solutions for roller bearing lubrication, monitoring, and assembly – with the goal of ensuring optimal machine operation and a particular focus on proper bearing lubrication, which can prevent many application problems.
Uncertainty and a lack of transparency in terms of actual lubricant volumes and the condition of conventional, automatic lubrication systems are often a reason for maintenance companies to continue applying lubricant manually rather than relying on automatic lubrication systems. As a result, up to 60% more lubricant is used than necessary.
The intelligently connected OPTIME C1 lubrication system was developed for automatic application of lubricant in larger machine parks – for example, in cement production and wood processing. The app and online dashboard provide a transparent overview of current machine conditions for hundreds of lubrication points at all times. A digital service offers assistance with optimal adjustment of lubricant volumes and remote monitoring of lubricant dispensers, which not only reduces grease consumption and any work associated with lubrication but also increases machine availability.
In addition to lubrication, condition monitoring can also contribute to efficient machine operation. The Schaeffler Group offers vibration-based condition monitoring solutions and services for this purpose, enabling early detection and prevention of machine failure or unfavorable operating conditions and thus reducing unplanned production downtime and losses.Part of NFB Ende
Industrial Automation
Part of NFBAs a development partner for customers in the sectors of medical technology, machine tools, robotics, foods, packaging, and general industrial machinery, the Schaeffler Group pursues sustainable progress with measures for increasing efficiency which includes innovative concepts for linear and rotary direct drives, with 30% less power loss and thus reduced energy requirements.
A typical application of this direct drive resulted in a reduction of 10,000 kWh per machine per year.
With the acquisition of Ewellix, the Industrial Automation department is also increasing its focus on highly efficient, electromechanical actuators to replace older technologies based on hydraulics, thereby doubling drive energy efficiency in many applications.
While maintaining the same performance data, RUE-F, a new generation of monorail guidance systems, was able to reduce the level of friction and thus drive power by up to 40% and lubricant consumption by an average of 30%.Part of NFB Ende
Cross-divisional approach to hydrogen
Part of NFBThe Schaeffler Group views hydrogen as a promising, renewable source of energy and raw material that is universal and suitable for storage and global transportation. Green hydrogen can also be used across all sectors, as it can supply different industry sectors and bring them together. Examples of the various applications include use as an electricity-based, industrial raw material for the steel and chemical industry, a stationary supply of electricity, and hydrogen-based electric mobility for road, rail, sea, and air.
The Schaeffler Group uses the opportunities provided by green hydrogen technology to develop its own products as well as decarbonize both the company and the supply chain. These activities are bundled at the hydrogen competence center in Herzogenaurach and managed by the internal “Schaeffler Hydrogen Council”. Made up of leading specialists and members of the Schaeffler AG Executive Board, the Council discusses the program’s progress on a quarterly basis and develops measures accordingly.
The Schaeffler Group’s cross-divisional approach is based on production expertise and further development of fuel cells and electrolyzers. With the industrialized production of these core technologies for green hydrogen, the Schaeffler Group aims to help expand availability and make it more cost-efficient. In addition, the company is preparing to use green hydrogen as a replacement for fossil fuels in internal production. For that reason, the Schaeffler Group is developing production capacities for green hydrogen at the Herzogenaurach and Schweinfurt locations, which also use their own electrolysis technology.
An electrolysis plant will be built in Herzogenaurach in partnership with the Lhyfe company and will supply green hydrogen not only to the Schaeffler headquarters and the hydrogen competence center, but also to the metropolitan region of Nuremberg.
The Schaeffler Group is also promoting the global development of a hydrogen infrastructure through its investment in the Hy24 Clean Infrastructure fund. The company is a guiding member in the global Hydrogen Council and is involved in additional European initiatives. The CEO of the Schaeffler Group’s Industrial division is also a member of the German National Hydrogen Council (NWR), which advises the German government on hydrogen issues.Part of NFB Ende
Fuel cells
Part of NFBThe Schaeffler Group firmly believes that hydrogen will play a key role in the sustainable mobility of the future, which is why the company relies on the fuel cell powertrain and efficient industrialization of the required technology. Collaboration in the “Innoplate” joint venture is an important step on this journey. The partnership aims to produce bipolar plates, which are key components of fuel cells, in large numbers in the future.
Currently under construction in Haguenau, France, the joint facility is expected to produce four million bipolar plates annually as of early 2024 and around 50 million plates a year by 2030. The Schaeffler Group is contributing to industrialization and series production with two of its most important technologies: high-precision forming and punching technology as well as innovative coating processes with internally developed coating recipes that address the specific requirements of fuel cells.
The Central Technology department is responsible for developing new material and coating solutions such as Enertect PC+, which is used in metallic bipolar plates to increase sustainability in hydrogen technology. This ultra-thin, non-precious metal coating in the nano to micrometer range makes it possible to use steel as a basic material rather than titanium or graphite. Steel is not only more affordable, but also easier to process, which simplifies large-scale series production. Compared to alternative, precious metal coatings, this coating reduces the carbon footprint by up to 99%. And thus the overall carbon footprint of the bipolar plate by around 20%. This process took second place in the 2022 CLEPA Innovation Award ceremony in the category “Clean and Sustainable Mobility”.Part of NFB Ende
Production of bipolar plates
Fuel cells are an important building block for the Schaeffler Group when it comes to achieving the goal of climate neutrality. A key component of fuel cells is bipolar plates. Watch the video to see how they are manufactured.
Electrolyzers
Part of NFBThe Industrial division supplies key components for electrolyzers, which are the underlying technology in the production of green hydrogen. The technologies and processes are similar to those associated with fuel cells. Both technologies benefit from the synergies of the jointly developed and used foundation in coating, material, and forming technologies.
The Schaeffler Group has also been involved in the government-funded H2 Giga program since 2021. As the consortium lead with industry and research partners, the company will further develop the future technology of electrolysis stacks, including the corresponding production processes, and promote industrialization through its activity in the Stack Industrialization Electrolysis (StacIE) subproject.
The StacIE consortium developed and successfully tested the first prototypes of proton exchange membrane (PEM) stacks in 2022. New material combinations and approaches to production address the efficiency of the electrolysis process, the scaling of the manufacturing process, and the sustainability of the materials used – with a particular focus on reducing utilization of rare metals such as iridium and platinum. The investments initiated at the end of 2021 led to the commissioning of three test benches at the hydrogen center in Herzogenaurach in 2022. Additional test benches have been ordered, with access scheduled for the first half of 2023.
This will further accelerate development of new electrolysis products at the hydrogen competence center in Herzogenaurach.Part of NFB Ende
Green hydrogen from seawater
The Schaeffler Group has been working systematically to develop solutions for producing the volumes of green hydrogen necessary for the energy transition. A new approach will enable the production of large volumes of green hydrogen at offshore wind farms.
Research and development
Part of NFBIn the area of research and development (R&D), the company employs 7,240 (prior year: 7,087)3) people at 20 R&D centers and additional R&D locations in a total of 25 countries. The company filed 1,8064) patent applications with the German Patent and Trademark Office in 2021. In addition, the Schaeffler Group employees internally reported 2,201 (prior year: 2,761) inventions in 2022.
In the reporting year, the new innovation strategy “Innovation-to-Business” was developed. It transfers the five global megatrends to focus areas and maps them in 6+2 innovation clusters. Strategic projects are selected via a portfolio review and then implemented in the business. Sustainability is an integral part of the Schaeffler Group’s innovation strategy.Part of NFB Ende
1) Key engine systems: timing drive, auxiliary drive, valve drive, and cooling system
2) The heat required for material hardening is generated by a coil that produces eddy currents locally in the workpiece. Because the heat is produced directly in the workpiece itself, it does not need to be transmitted via convection, radiation, or thermal conduction.
3) Workforce values are provided as full-time equivalents (FTEs); reporting date of 31/12/2022. The 2021 value has been adjusted.
4) The patent applications are first filings in Germany.