Energy and emissions
- The Schaeffler Group has expanded its climate neutrality target to include the supply chain
- In 2021, the energy efficiency program focused, e.g., on optimizing production systems and processes
Climate neutrality by 2040
Bestandteil des GNFK StartClimate change is one of the world’s most pressing challenges, which is why the Schaeffler Group is making every effort to significantly reduce its climate impact. Internal production (Scope 1 and 2) will be climate-neutral as of 2030, with 75 % of production emissions eliminated by 2025. The emissions resulting from intermediates and raw materials in the supply chain (Scope 3 upstream) will be reduced by 25 % by 2030. The Schaeffler Group will also be climate-neutral in this area by 2040. The base year for all calculations is 2019. Efforts to achieve these targets will focus on reduction measures, and only unavoidable emissions will be offset with compensation measures.
The company also pursues a climate program that systematically and methodically monitors all divisions, functions, and regions, and is based on three pillars: sustainable materials, production, and products. The sustainable materials pillar includes all climate-relevant measures of sustainable procurement, including dialogues with strategically relevant steel suppliers about their climate performance and sustainable logistics and packaging. Most importantly, the sustainable production pillar encompasses the Sustainable Sites initiative, which strengthens the sustainability performance of all production sites. The sustainable products pillar addresses topics such as life cycle assessments and product innovations for an improved carbon footprint.Bestandteil des GNFK Ende
Climate-neutral company by 20401)
1) Target includes the entire supply chain as well as the company's own production (Scope 1 and 2).
Focus areas
Product design
Life cycle analyses show the carbon footprint of a product and make it possible to derive optimization measures, such as:
- Optimized selection of materials (materials with low specific footprint and avoidance of “critical raw materials”)
- More efficient use of materials (high material utilization, prevention of scrap)
- Improved energy efficiency in application – e.g., through friction reduction
- Simplified reuse, reparability and recyclability
Green steel
- Analysis of decarbonization strategies of the global steel industry
- Request for information, monitoring and documentation of CO2 emissions from the most important steel suppliers
- Initiation of activities to switch to CO2-reduced steel for products
- Agreement signed with Swedish start-up H2greensteel for the sustainable supply of steel
Renewable energy
- Since 2021, all European production sites have been purchasing electricity exclusively from renewable sources
- Generation of own renewable energy is being expanded at several sites – e.g., Szombathely, Salvi, Taicang
Energy efficiency
- Energy-efficient solutions optimize buildings and their supply systems
- Optimization of the energy consumption of production processes, manufacturing machinery and central systems
- Establishment of Schaeffler Exchange on Climate Technologies as a global platform for the exchange of best practices, technological developments and inspiration
Sustainable logistics
- Monitoring of CO2 emissions in transport
- Incorporation of CO2 emissions caused by transport into the strategic planning and optimization of own supply chain
- Implementation of a uniform CO2 calculation instrument for all modes of transport
Life cycle assessment
- Standardized analysis of the carbon footprint of Schaeffler products
- The LCA methods and life cycle assessments of individual products were certified by TÜV Rheinland
- Conduct of scenario analyses to identify CO2 optimization potential, including for selected Schaeffler products
Life cycle assessments
The Schaeffler Group conducts life cycle assessments (LCAs) to determine the environmental impact of products throughout their entire life cycle. Based on the ISO 14040 and ISO 14044 standards, internal guidelines were developed to regulate LCA administration, processing, reporting, and more. These methods were certified by TÜV Rheinland in 2021. The LCAs serve as a central tool for documenting the sustainability performance of products and processes. With a particular focus on a product’s carbon footprint, the corresponding focus areas in the supply chain and in production can be identified, and suitable reduction measures derived.
Life Cycle Assessment
Click for more
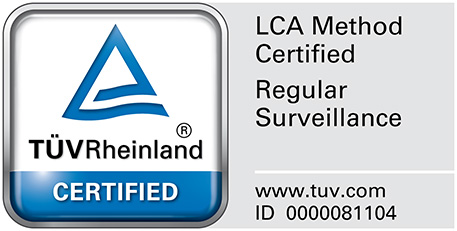
LCA software
The LCA software used is based on the ISO 14040 and ISO 14044 standards, which govern life cycle analyses. All values calculated are incorporated into a comprehensive life cycle assessment model and form the basis for assessment and optimization of the carbon footprint.
Innovation
Ongoing improvement of existing products and development of pioneering, sustainable products and systems are the pillars of the corporate philosophy, with a focus on sustainable use of energy and raw materials – during product development, production, utilization, and recycling.
Raw materials and suppliers
The company works with suppliers to document all data associated with the raw materials and energy that go into a product, all the while observing the LCA-defined standards and relying on the best possible data quality. The internal LCA databases also provide access to internationally comparable secondary data.
Production
Data collection is continued throughout the entire Schaeffler production chain for relevant process steps and is broken down for the energy sources and raw, auxiliary, operating, and other materials used.
Logistics
A key aspect in the calculation of a product’s life cycle assessment is logistics – e.g., transport from the production sites to the customer, depending on the order. These data are also documented in the LCA software.
Utilization
The utilization of products generally leads to indirect emissions resulting, e.g., from product weight or friction loss. As a result, the company tries to minimize the indirect share of emissions even during the development phase, with forward-looking and innovative thinking.
Recycling
Even in the early stage of product development and construction, the company focuses on repairs, recycling, and smart reuse. These activities represent good opportunities to extend the service life of products and thus significantly improve their life cycle assessment; this is an approach used by Automotive Aftermarket and other business units.
Generating green electricity
Bestandteil des GNFK Start The existing photovoltaic systems at the locations in Kitzingen and Pune were joined in 2021 by new photovoltaic systems in Savli and Szombathely. The Schaeffler Group thus has its own solar power systems with output of around 2,285 kWp.Bestandteil des GNFK Ende
Increasing energy efficiency
Bestandteil des GNFK Start Our fundamental aim is to increase energy efficiency. The Schaeffler Group’s energy management defines minimum targets for all plants, which in turn set their own targets, with implementation assessed through internal and external Energy, Environment, Health and Safety (EnEHS) audits.
The company-wide documentation of energy consumption and an internally defined management approach form the basis for ongoing improvement in the area of energy efficiency. The Schaeffler Group also works with a globally standardized energy management system based on ISO 50001, which achieved a coverage rate1) of 100 % in 2021 (prior year: 99.3 %). Internal energy representatives and auditors monitor consumption trends.
Around 47 GWh
of cumulative annual energy savings will be achieved starting in 2022
In 2020, the Schaeffler Group started bundling all relevant resources in a single energy efficiency program with an interdisciplinary team on a plant, regional, and central level for the purpose of increasing cumulative annual energy efficiency by 100 GWh by 2024. The sub-target for 2021 was to ensure that the 2020 and 2021 energy efficiency measures would lead to cumulative annual savings of at least 45 GWh starting in 2022. During the reporting year, 104 further measures achieved cumulative improvements of 46.8 GWh worldwide. Measures included intelligent LED lighting concepts as well as optimizing heating and compressed-air systems. There was an increased focus on optimizing production systems and processes, including improved thermal insulation and the use of more efficient electric drives.
|
|
2021 |
|
2020 |
|
2019 |
||||||||||||||
---|---|---|---|---|---|---|---|---|---|---|---|---|---|---|---|---|---|---|---|---|
Total energy consumption1) 2) 6) |
|
3,412 |
|
3,045 |
|
3,290 |
||||||||||||||
Electricity consumption2) 3) 6) |
|
2,242 |
|
2,078 |
|
2,316 |
||||||||||||||
Conventional energy (CHP)4) |
|
46 |
|
– |
|
– |
||||||||||||||
Natural gas/LPG consumption2) 5) 6) |
|
925 |
|
830 |
|
872 |
||||||||||||||
Fuel oil consumption2) |
|
6 |
|
6 |
|
7 |
||||||||||||||
District heating consumption2) 6) |
|
57 |
|
49 |
|
48 |
||||||||||||||
Propane consumption2) 5) 6) |
|
52 |
|
45 |
|
– |
||||||||||||||
Methanol4) |
|
84 |
|
– |
|
– |
||||||||||||||
|
Reducing CO2 emissions
Bestandteil des GNFK StartAs a result of ongoing improvement in energy efficiency and the increased share of renewable energies, the Schaeffler Group’s production-related CO2 emissions2) fell by around 6 % from 744 thousand tons of CO2 to 703 thousand tons of CO2 compared to the prior year.
In the year under review, emission values were calculated for all raw and other materials purchased, focus areas were identified, and potential for reduction was developed – all to achieve a climate-neutral supply chain by 2040 and reduce emissions by at least 25 % until 2030 (base year 2019).
Own greenhouse gas emissions in thousand t CO2, including Scope 1 and Scope 2 (market-based)1) 2)
1) The calculation of greenhouse gas emissions is based on the emission factors of the VDA (2017) and the ProBas database of the German Federal Environmental Agency. Emission sources covered: Scope 1 (natural gas, fuel oil, propane, methanol) and Scope 2 (electricity, district heating). 2020 and 2019 values excl. methanol. The emission factors for natural gas were adjusted for the locations that supply and invoice natural gas based on calorific value.
2) Supplier-specific emission factors were used to determine Scope 2 (market-based).
Due to Schaeffler’s product portfolio, the procurement of steel plays a key role as a driver for CO2 emissions. According to the latest information, steel can be produced more sustainably using green hydrogen. Over the short to medium term, however, other measures will be necessary to reduce Scope 3 upstream emissions. As a result of the large volume of steel used in Schaeffler products, a working group is conducting an analysis of the primary influential factors relevant for using steel. The steel manufacturers’ decarbonization strategies are evaluated and categorized to accommodate developments in the global supplier base. Recommended courses of action are then developed to reduce Scope 3 emissions related to steel over the long term.
Total greenhouse gas emissions, including Scope 1, Scope 2 (market-based), and Scope 31) in thousand t CO2
1) The calculation of Scope 3 currently includes four upstream categories.
2) The calculation of greenhouse gas emissions is based on the emission factors of the VDA (2017) and the ProBas database of the German Federal Environmental Agency. Emission sources covered: Scope 1 (natural gas, fuel oil, propane, methanol) and Scope 2 (electricity, district heating). Supplier-specific emission factors were used to determine Scope 2 (market-based).
3) Scope 3.1, Scope 3.4, and Scope 3.5 greenhouse gas emissions are calculated based on a recognized input-output model that uses the method of multiregional input-output calculation and quality-assured data from international environmental, resource, and social statistics (OECD, BEA, World Bank indicators, and EXIOBASE). Calculation is based on Schaeffler’s purchasing volume in 2021 and takes additional steel-specific factors into account.
4) Not contained in Scope 1 or 2. Scope 3.3 greenhouse gas emissions are calculated based on the emission factors of Defra (2022) and the emission factors of the German Federal Environmental Agency (2021, emission values of renewable energy sources). Upstream chain emissions and T&D losses are calculated based on the emission sources considered for Scope 1 (natural gas, fuel oil, propane, methanol) and Scope 2 (electricity, district heating).
5) The 2021 value is based on a current projection
The company talks to suppliers to monitor concrete steps for reducing production-related CO2 emissions and to verify their feasibility. Concepts are also being developed that consider efforts to achieve a circular economy and increase the use of green energy.
At the end of 2021, the Schaeffler Group agreed to procure 100,000 tons of nearly carbon-free, hydrogen-produced steel annually from Swedish start-up H2greensteel beginning in 2025. The steel produced in Sweden does not require any fossil fuels, and under equal conditions, reduces the Schaeffler Group’s annual CO2 emissions by up to 200,000 tons. This agreement represents the first important step towards making the company’s supply chain climate-neutral by 2040.Bestandteil des GNFK Ende
1) Relating to employees on the production sites.
2) The calculation of greenhouse gas emissions is based on the emission factors of the VDA (2017) and the Probas database of the German Federal Environmental Agency. Emission sources covered: Scope 1 (natural gas, fuel oil, propane, methanol) and Scope 2 (electricity, district heating). Total of Scope 1 and Scope 2 (market-based). The 2020 value has been adjusted.