FOCUS ON
CLIMATE-NEUTRAL
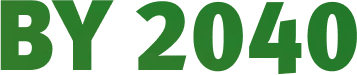
The Schaeffler Group is increasing its efforts to ensure effective climate protection: The company’s targets are climate-neutral procurement of intermediates and raw materials by 2040 and climate-neutral production by 2030, primarily on the basis of reduction measures and the use of renewable energies.
By using of solar energy – as illustrated with solar panels at the location in Kitzingen – Schaeffler makes an important contribution to climate protection.
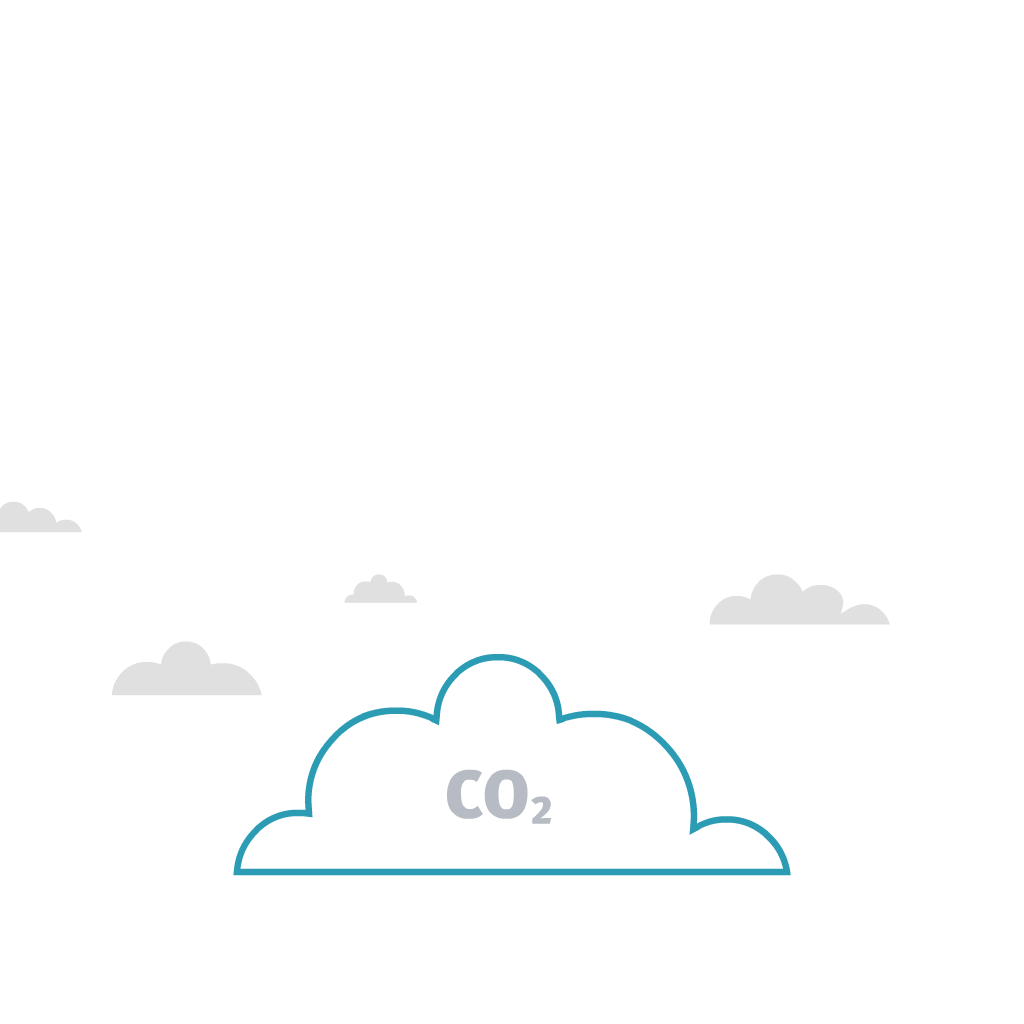
reduction in emissions resulting from in-house production by 2025.
Clear milestones set
As one of the world’s leading industrial and automotive suppliers, Schaeffler develops solutions and components for a sustainable energy and mobility transition. The aim is to produce climate-neutral by 2030 and reduce production emissions by three-quarters by 20251) – e.g., by focusing on energy efficiency measures and the use of renewable energies.
1) The base year for all calculations is 2019.
Decarbonizing the Schaeffler Group and its supply chain is our top priority. Therefore, we have set ourselves specific reduction targets.
Thomas Fußhöller Head of Sustainability & EHS
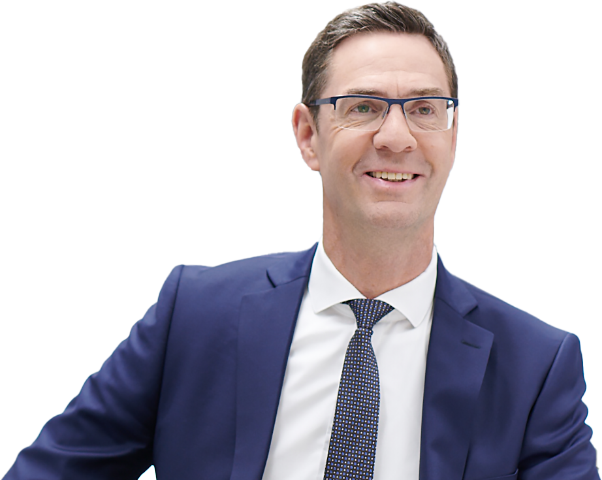
Renewable energies and energy efficiency as a basis
To achieve the climate target for in-house production, Schaeffler is primarily increasing energy efficiency and procuring green electricity. All German production sites have been purchasing 100 percent of their electricity from renewable sources since 2020, and all European sites since 2021. By 2024, every site worldwide will source 100 percent of its electricity from renewable energies.
In addition to using renewable energies, the Schaeffler energy efficiency program makes a key contribution to achieving climate neutrality: An increase in energy efficiency of 100 gigawatt hours is to be achieved by 2024. The measures implemented in 2020 and 2021 will lead to cumulative annual savings of 46.8 gigawatt hours starting in 2022. This is equivalent to the annual electricity consump-tion of approximately 15,000 two-person households in Germany.
of energy purchased at all European production sites from renewable sources
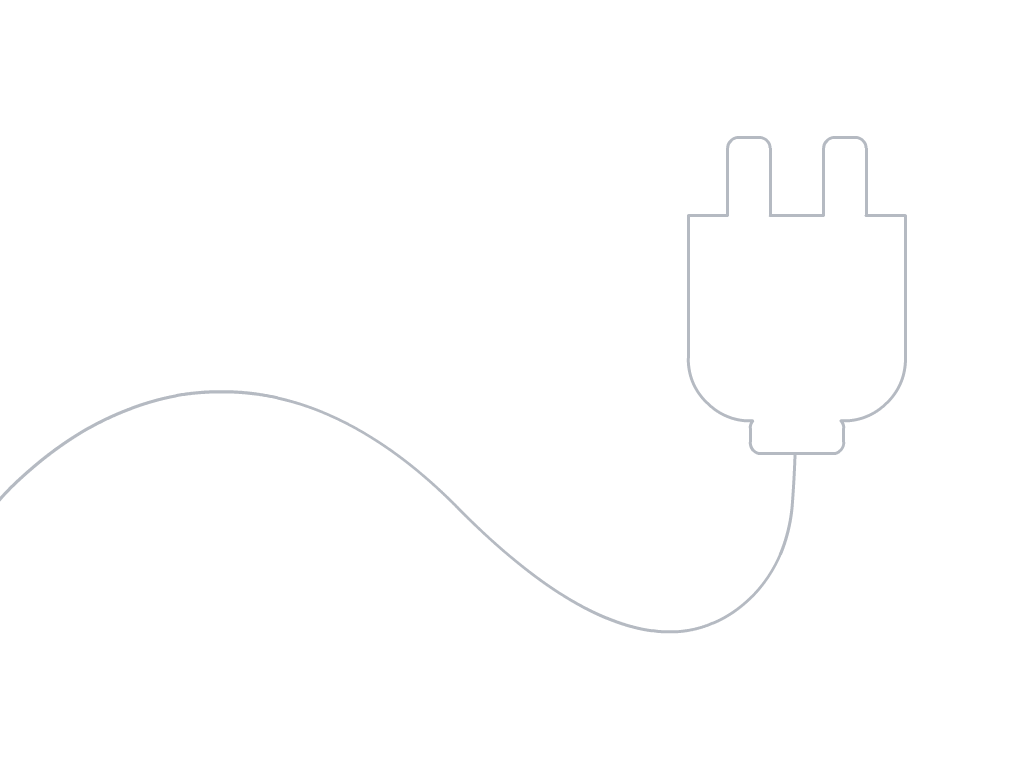
Intelligent LED lighting projects are just part of the numerous measures of the energy efficiency program.
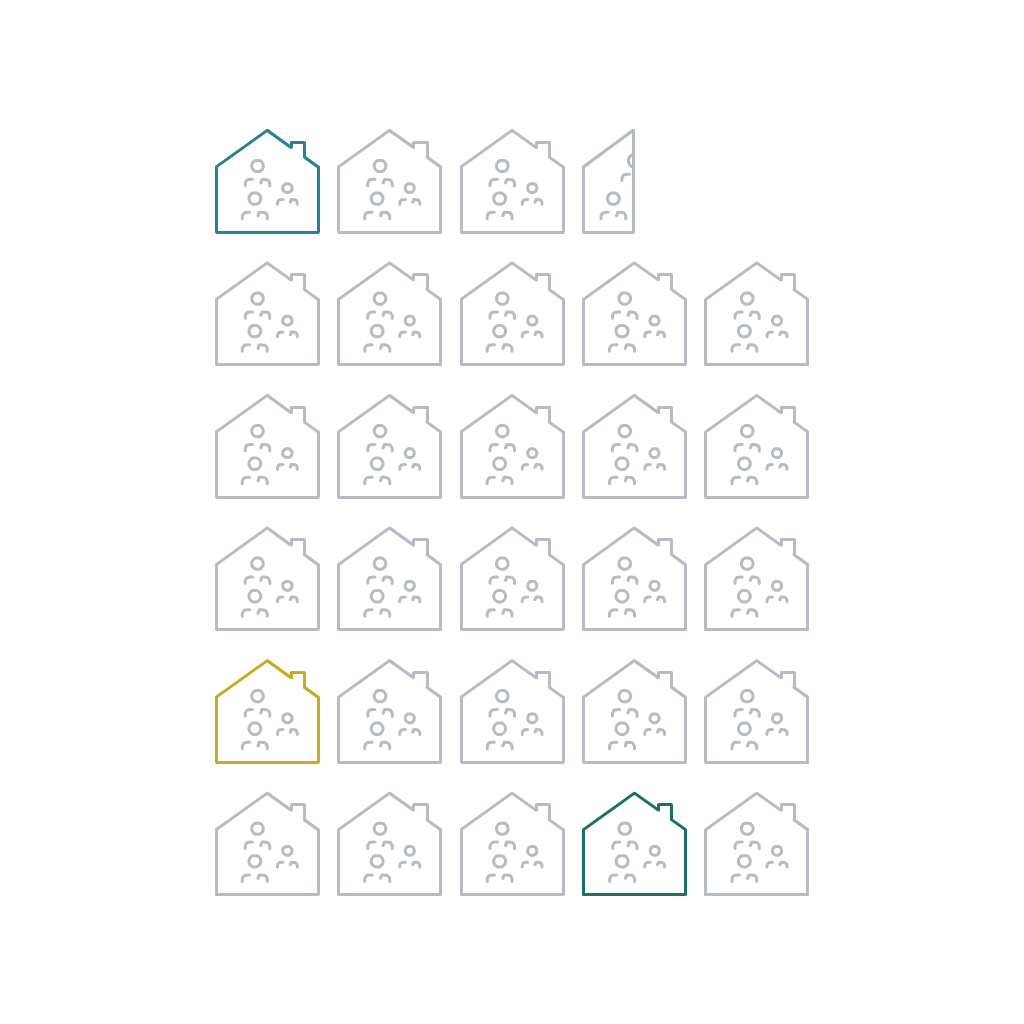
Energy savings by 2022 are equivalent to the annual electricity consumption of
two-person households
in Germany
Expanding sustainable production
In addition to renewable energies and improved energy efficiency, the sustainable production of tomorrow also requires careful use of resources and maximum safety standards for employees at the workplace. In an effort to continuously improve sustainability performance at all production sites, Schaeffler launched the “Sustainable Sites” initiative in 2020. Its aim is to systematically evaluate plants in accordance with consistently defined sustainability requirements as well as to implement measures to advance environmental and social aspects. Implementation is already underway at numerous existing production sites and in the construction of new ones.
Markets expect acceleration in ESG progress, and we are committed to it. All of us take action to reach our sustainability targets, as well as delivering long-term profitable growth
Renata Casaro Head of Investor Relations
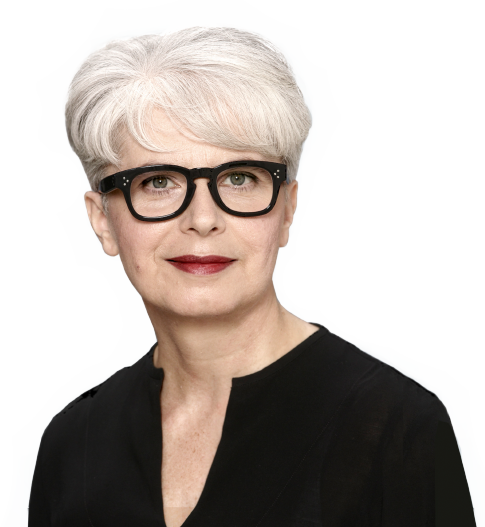
The new production site in Szombathely in Western Hungary is the Schaeffler Group’s first plant dedicated entirely to e-mobility.
Groundbreaking plant in Hungary
With its new e-mobility plant in Szombathely, Hungary, Schaeffler has achieved one of its milestones for future-proof manufacturing. In combination with the primary plant for e-mobility in Bühl, Germany, the Schaeffler Group’s first dedi-cated e-mobility plant forms the new competence center for the production of components and systems for electric drives. The plant features a high degree of automation, while the halls boast a modular design and are digitalized through-out. The new plant uses solar energy and thus makes a key contribution to reducing CO2 emissions.
But Schaeffler is not only focusing on reducing emissions. It is also optimizing its consumption of resources: The reuse of treated wastewater and a rainwater retention basin preserve natural resources. Heat recovery heat pumps as well as intelligent heating and cooling management systems maximize energy efficiency. In addition, intelligent LED lighting not only reduces energy consumption, but also ensures perfect illumination of the work environment. The German Sustainable Building Council (DGNB) has certified the plant with Gold status.
With the plant in Szombathely, we are not only contributing to our target of climate neutrality, but also optimizing our use of resources – e.g., by treating rain-water and wastewater and using it in our production processes.
Tibor Szigeti Managing Director Schaeffler Savaria
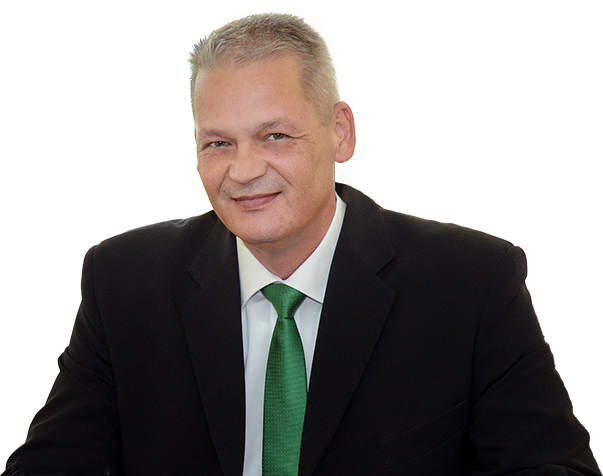
As of 2025, Schaeffler will purchase 100,000 tons of steel annually that stems from an almost entirely carbon-free production process.
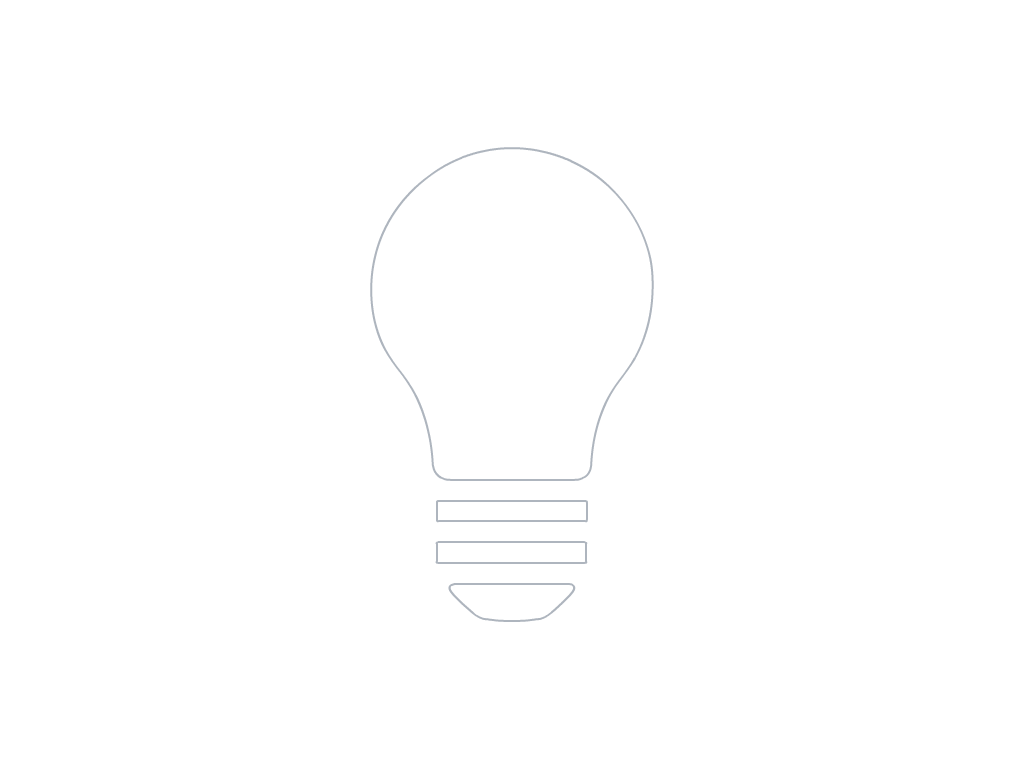
tons of CO2
will be reduced annually through the collaboration with H2greensteel
Climate targets extended to the supply chain
Schaeffler has also included its supply chain in its climate-friendly transfor-mation: The emissions resulting from intermediates and raw materials will be reduced by 25 percent by 2030. The company plans to be entirely climate-neutral by 2040, with carbon offsetting only being used where any residual emissions are unavoidable.
Green steel as a central lever in the supply chain
A majority of the Schaeffler Group’s emissions occur in the supply chain. Especially steel plays a key role, as it is required for the manufacturing of numerous products. Raw materials and intermediates will be acquired using more climate-friendly processes in the future, which will prove to be a challenge particularly in high-energy areas such as steel and aluminum production. Schaeffler is breaking new ground to increase the availability of green steel and other sustainably produced raw materials: The company concluded an agreement with the Swedish start-up H2greensteel in 2021 and, as of 2025, will purchase 100,000 tons of steel annually that stems from an almost entirely carbon-free production process based on hydrogen. This alone will reduce Schaeffler’s CO2 emissions by up to 200,000 tons per year, bringing the company one big step closer to its target of a climate-neutral supply chain by 2040.
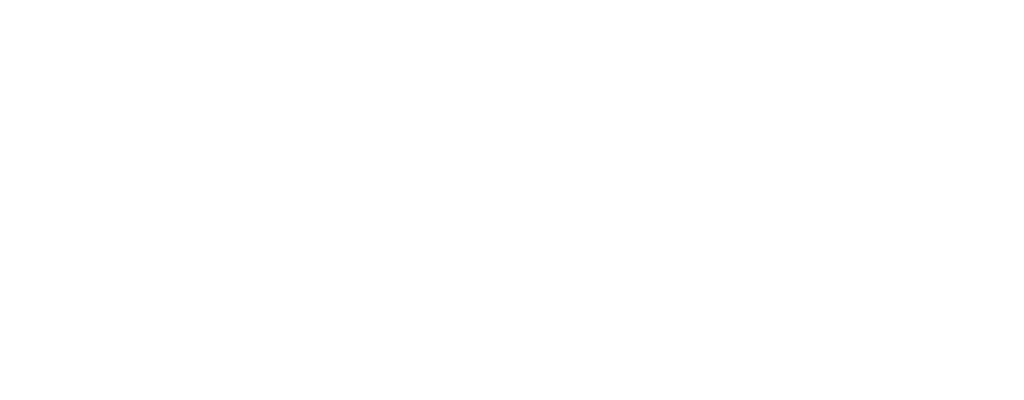
The procurement of green steel is an important milestone on our path to a climate-neutral supply chain.
Martin Santer Vice President Corporate Purchasing Production Material
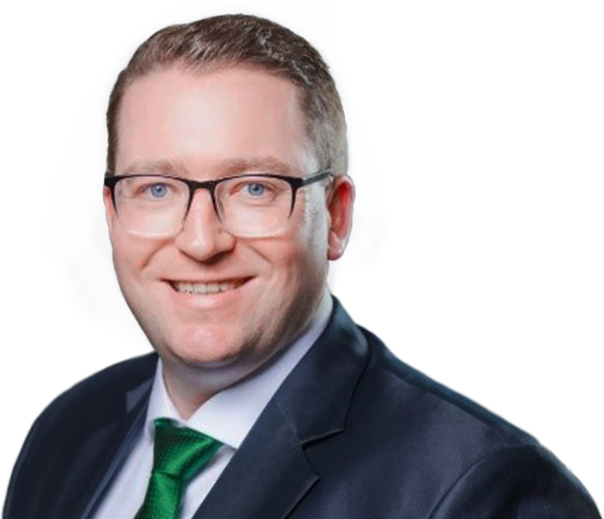