Climate and environmental protection begins in the company.
Being a pioneer – we pursue this goal not only with our products, but also with environmentally friendly, energy and resource-efficient production processes. An ambitious environmental and energy policy that is harmonized worldwide creates the basis for this.
“Sustainable Factory” subprojects were launched as part of the “Factory for Tomorrow” initiative within the program for the future “Agenda 4 plus One”.
Where we stand
We asked the project managers for their subjective assessment:
How far along is the pilot testing of the CO2-neutral factory?
How much of the potential of 3D printing technology has Schaeffler already exploited?
Coverage rate of production sites with energy management certification ISO 500011)
We control our activities with company-wide energy and environmental management systems. Their implementation is audited by independent experts.
1) Relating to employees
Our goal: the sustainable factory
We are constantly working on improving our production processes, for example through systematic energy management, using resource and material-saving technologies, or avoiding respectively recycling production waste. With the concept of the “Sustainable Factory”, we are pursuing a holistic approach. For example, manufacturing and logistics processes are digitalized so that machines and processes can be controlled centrally and optimized with regard to their efficiency. The approach also includes sustainability standards for procuring production machinery and constructing new buildings.
Last but not least, the needs of our employees are also taken into account. The architecture and the equipment of the “Factory for Tomorrow” support flexible work processes and encourage personal interaction. You can find more on these topics under “Environment and energy”.
Delivery, temporary storage and distribution under one roof – the central goods receiving area in Herzogenaurach is ideally suited as a pilot project for sustainable energy production, storage, and use. All processes will run around the clock with solar energy in the future.
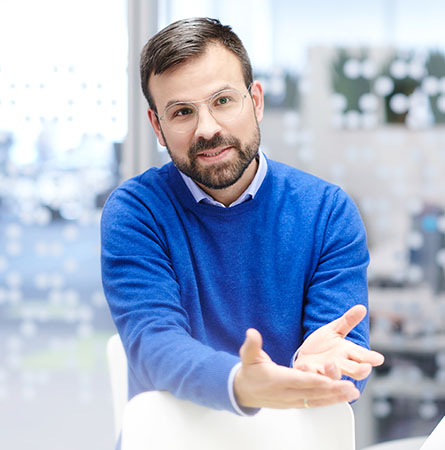
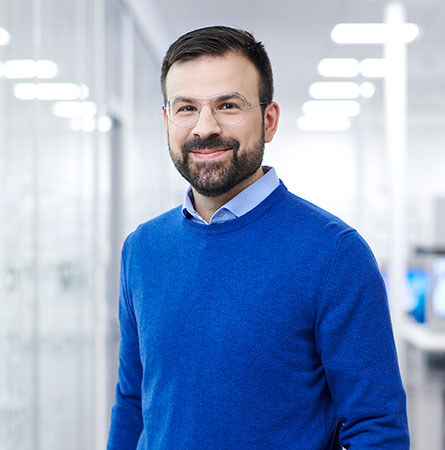
“Our product innovations are not only an asset for our customers. Thanks to our new power storage, we want to supply the ‘Sustainable Factory’ steadily with green electricity.” Christian Adler, Corporate Factory Planning, Head of Workstream Sustainable Factory
A solar energy system will be built on the roof of the goods receiving area. It will cover the energy needs of the building and also provide power for charging stations and for producing hydrogen for fuel cells. “In order for the electricity to flow even when the sun is not shining, we rely on scalable storage technology from a joint venture,” explains Adler. This technology is based on renewable raw materials and is about to be ready for the market.
High-quality components from the laser printer? Additive manufacturing – also called 3D printing – is what processes are called in which workpieces are no longer machined out of a solid block, but rather built up layer by layer from a powdery raw material among other things.
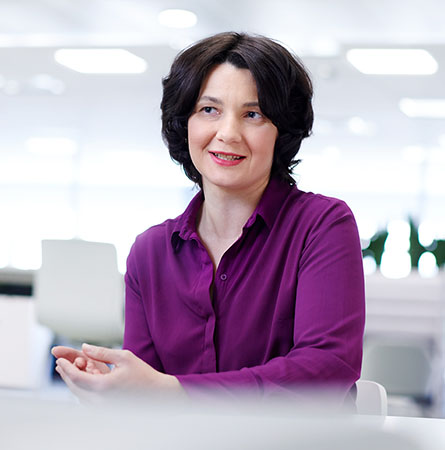
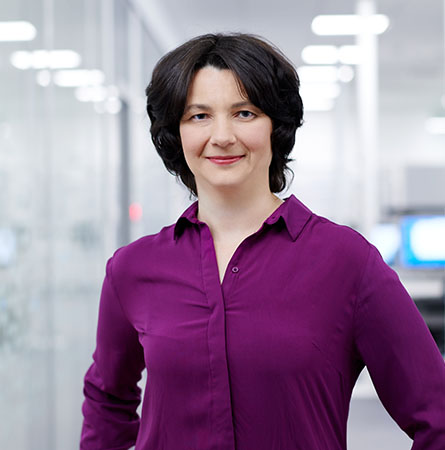
“The potential of additive manufacturing is far from exhausted. When used properly, we can achieve significant material, cost, and time savings.” Ruslana Mys, Development Production Technology Specialist
Every year, Schaeffler produces around 5,000 parts in Herzogenaurach via additive manufacturing – and the trend is increasing. “Not only representative samples are produced in this way, but also high-quality prototypes and tools for series production,” reports Mys. In 2015, we established our own additive manufacturing department and are constantly developing new application possibilities.
Additive methods have an advantage
The so-called “double comb cage” is a cylindrical hollow body that is used in roller bearings. Using additive methods saves 14.5 kg of material for the blank.