We act responsibly – within the company and along the supply chain.
Integrity, fairness and mutual respect – these are the values that our corporate activity is based on. We take our responsibility seriously and act in accordance with the law and regulations at all times. In so doing, we create the foundation for sustainable corporate success.
Around
suppliers from 82 countries carried out work for the Schaeffler Group in 2018.
Where we stand
We asked the project managers for their subjective assessment:
How satisfied are the employees in India with the combined compliance training concept?
How far along is the first pilot of a global audit standard?
Response rate of surveyed suppliers on the use of conflict minerals1) 2)
Schaeffler tracks the regions from which subcontractors purchase components containing critical raw materials in order to initiate targeted measures in the supply chain where appropriate.
1) Response rate of relevant suppliers surveyed on the use of conflict minerals as defined under the Responsible Minerals Initiative.
2) Survey period from March to February of the following year.
Worldwide responsibility
The Schaeffler Group expects integrity and law-abiding behavior from all employees and executives. We clearly express these requirements in our Code of Conduct. The requirements are not only aimed at our own organization, but also at our suppliers.
As an international automotive and industrial supplier, we work with a globally branched supply chain. Making this supply chain responsible in terms of human rights and environmental and social aspects is part of our sustainable corporate leadership. In our Supplier Code of Conduct, which every new supplier has to sign, we have stipulated the corresponding requirements. In addition, we subject potential suppliers to a systematic selection process in which sustainability aspects are also questioned. You can find more on these topics under “Sustainable management”.
How do I put the requirements of the Schaeffler Code of Conduct into practice in my everyday activities? We support our employees by offering practical training. The training includes realistic situations based on concrete case studies.
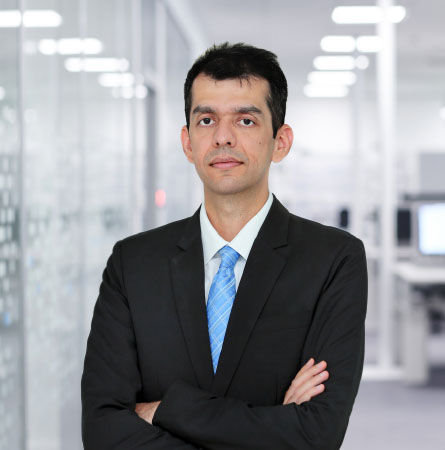
“We have created a culture of compliance in which our employees are actively involved. Our training is continually adapted to new requirements.” Abhay Jhina, Regional Compliance Officer India
Our compliance training method combines e-learning with face-to-face training. The foundation training on our Code of Conduct, which is obligatory for all employees, takes place online and is available in 14 languages. “This raises awareness of compliance issues. But that alone is not enough,” states Abhay Jhina. “In face-to-face training, we can answer individual questions flexibly, personally and effectively.”
Perfect combination
We complement our online compliance foundation training with individual face-to-face sessions. This lets us use the advantages of both methods and ensure long-term learning success.
Total participants3) in compliance training in 2018
Participants in compliance training in India
3) Employees incl. temporary staff, apprentices, interns, and contract workers.
We are taking the initiative in China and have launched a pilot project to outline a new global standard for supplier audits. The aim is to ensure that human rights, safe working conditions, and strict environmental laws and regulations have been adhered to.
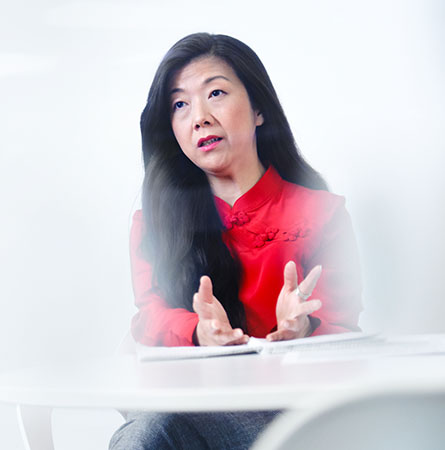
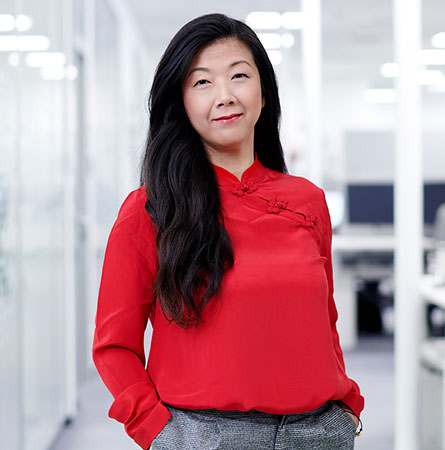
“It is our duty to audit our supply chain thoroughly according to sustainability criteria. We are facing a challenging situation in China at the moment.” Yan Chen, Director Supplier Quality Management, Purchasing, Schaeffler Greater China
In 2017, environmental laws and regulations became much stricter for companies in China. “We have expanded the scope of our supplier audits as a result of these changes,” Yan Chen reports. “But, for us, it is not enough simply to check environmental aspects.” Yan Chen’s team also expanded the audit log to include the industry-specific social requirements of the German Association of the Automotive Industry (VDA), for example, in relation to working conditions.
Sustainability and purchasing
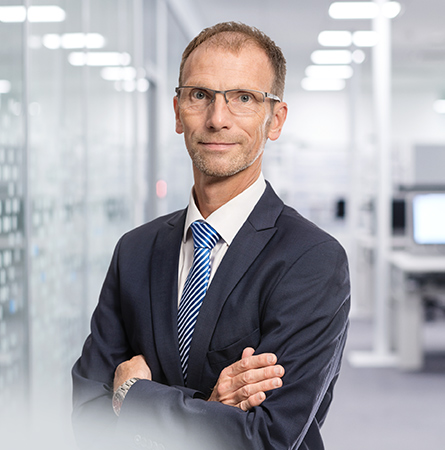
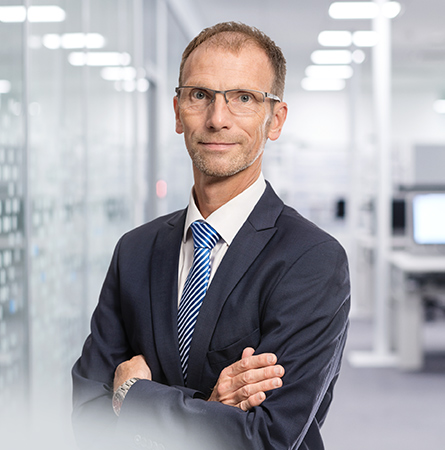
“We can only meet increasing expectations by working together.” Achim Döll, Senior Vice President Purchasing & Supplier Management Sustainability
“The expectations of society and our customers regarding a sustainable supply chain continue to increase. Our purchasers must know exactly how to meet their needs. For this reason, we continually expand the necessary skill sets,” says Achim Döll. As at May 1, 2019, Schaeffler created the new central function of Purchasing & Supplier Management Sustainability.
Achim Döll and his team are contact partners for all sustainability questions related to the supply chain. They develop strategic concepts, assist in implementing guidelines, standards, and customer requirements, and make recommendations to involved departments. “In our work, in addition to the purchasing department, we exchange information with other business divisions and functions worldwide – for example, with Yan Chen”, explains Achim Döll. “Moreover, we coordinate our strategy and the resulting sustainability goals, measures and indicators with the sustainability division, and develop customer-oriented solutions.”
Extensive audits
In 2018, we audited around one tenth of all suppliers based in China as part of an obligatory EHS audit. These audits covered environmental, health, and occupational safety aspects.
Suppliers based in China
Suppliers audited on environmental and occupational health and safety topics in 2018 in China
Audits planned as part of pilot project in 2019